Fabry-Perotw fiber-optic pressure sensor and manufacture method therefor
A pressure sensor, Perot-type technology, applied in the field of Fabry-Perot-type optical fiber pressure sensors, can solve the problems of difficult demodulation, small air cavity size, difficult signal demodulation, etc., and achieves good reliability and easy production. , the effect of high sensitivity
- Summary
- Abstract
- Description
- Claims
- Application Information
AI Technical Summary
Problems solved by technology
Method used
Image
Examples
Embodiment 1
[0032] The silicon is thinned to 180 microns thick by a wet etch method. The glass tube was cut to a length of 3.2 mm, after which both end faces of the glass tube were polished. The glass tube is stacked on the silicon wafer and then placed in the bonding furnace, which is heated to 300°C. The silicon chip is connected to the positive pole, the glass tube is connected to the negative pole, and the voltage is slowly increased to 800V. When the current is zero, take out the glass tube and the silicon wafer, and the two have become one. Place the bonded glass tube in the groove of the FOCI-type optical fiber flange, and fix the side wall with epoxy resin for 24 hours. Screw the FC-PC optical fiber plug to the optical fiber flange (1), the ceramic ferrule (2) on the optical fiber plug and the lower surface of the single crystal silicon wafer (4) form a Fabry-Perot cavity, and finally The sensor is completed by installing the flange plate on the base of the packaging sleeve. ...
Embodiment 2
[0034] The silicon is thinned to 180 microns thick by a wet etch method. The glass tube was cut to a length of 3.2 mm, after which both end faces of the glass tube were polished. The glass tube is stacked on the silicon wafer and then placed in the bonding furnace, which is heated to 300°C. The silicon chip is connected to the positive pole, the glass tube is connected to the negative pole, and the voltage is slowly increased to 800V. When the current is zero, take out the glass tube and the silicon wafer, and the two have become one. Place the bonded glass tube in the groove of the FOCI-type optical fiber flange, and fix the side wall with epoxy resin for 24 hours. Screw the FC-PC optical fiber plug to the optical fiber flange (1), the ceramic ferrule (2) on the optical fiber plug and the lower surface of the single crystal silicon wafer (4) form a Fabry-Perot cavity, and finally The sensor is completed by installing the flange plate on the base of the packaging sleeve. ...
Embodiment 3
[0036] The silicon is thinned to 150 microns thick by a wet etch method. The glass tube was cut to a length of 3.2 mm, after which both end faces of the glass tube were polished. The glass tube is stacked on the silicon wafer and then placed in the bonding furnace, which is heated to 300°C. The silicon chip is connected to the positive pole, the glass tube is connected to the negative pole, and the voltage is slowly increased to 800V. When the current is zero, take out the glass tube and the silicon wafer, and the two have become one. Place the bonded glass tube in the groove of the FOCI-type optical fiber flange, and fix the side wall with epoxy resin for 24 hours. Screw the FC-PC fiber optic plug to the fiber optic flange (1), the ceramic ferrule (2) on the fiber optic plug and the lower surface of the single crystal silicon wafer (4) form a Fabry-Perot cavity, and finally The sensor is completed by installing the flange plate on the base of the packaging sleeve. Lap th...
PUM
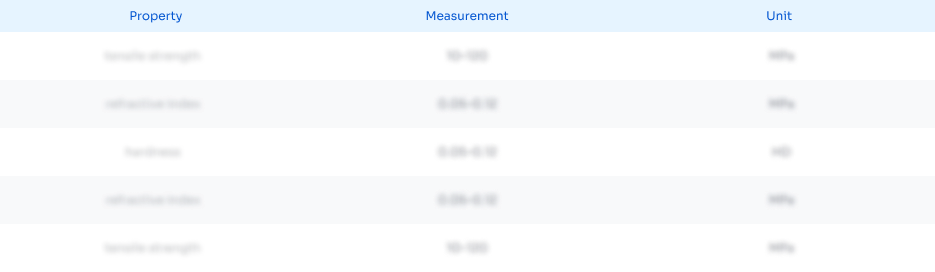
Abstract
Description
Claims
Application Information

- R&D
- Intellectual Property
- Life Sciences
- Materials
- Tech Scout
- Unparalleled Data Quality
- Higher Quality Content
- 60% Fewer Hallucinations
Browse by: Latest US Patents, China's latest patents, Technical Efficacy Thesaurus, Application Domain, Technology Topic, Popular Technical Reports.
© 2025 PatSnap. All rights reserved.Legal|Privacy policy|Modern Slavery Act Transparency Statement|Sitemap|About US| Contact US: help@patsnap.com