Process of preparing alkyl dead-end polyether by polyether with parahydroxyl at molecular chain end
A technology of alkyl end-capping and molecular chain, which is applied in the synthesis field of end-capping polyether, and can solve the problem of low end-capping rate
- Summary
- Abstract
- Description
- Claims
- Application Information
AI Technical Summary
Problems solved by technology
Method used
Image
Examples
Embodiment 1
[0027] Add 400 g of allyl alcohol polyoxypropylene ether (hydroxyl value 73) and 188 g of alcoholic solution of sodium methylate in a 1000 ml round bottom flask equipped with an electronic constant speed stirrer, a reflux condenser, a thermometer and a dropping funnel. Under the condition of -0.085~-0.098, react at 90~95°C for 1 hour, cool down to 45~50°C, add 164g of bromobutane dropwise, and finish dropping in about 3 hours. After the dropwise addition, continue to react at 45~50°C for 4 hours. Add 200g of water, stir at 40-45°C for 0.5 hours, then let stand to separate layers, remove the water phase, neutralize with alkali until the pH is 6-8, dehydrate in vacuum, add diatomaceous earth filter aid and filter to obtain alkyl End-capped polyether products.
Embodiment 2
[0031] Add allyl alcohol polyether (EO / PO=55 / 45, block, PO chain segment at the end, hydroxyl The value is 36) 600g, 176g of alcohol solution of sodium methoxide, under the condition of vacuum degree of -0.085~-0.098, react at 90~95°C for 1 hour, cool down to 40~45°C, add 148g of bromobutane dropwise, drop for about 3 hours After completion of the dropwise addition, the reaction was continued at 40-45°C for 4 hours. Add 300g of water, stir at 40-45°C for 0.5 hours, then let stand to separate layers, remove the water phase, neutralize with alkali until the pH is 6-8, vacuum dehydrate, add diatomaceous earth filter aid and filter to obtain alkyl End-capped polyether products.
PUM
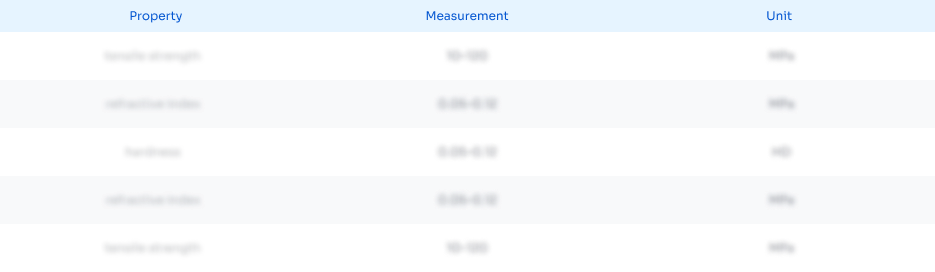
Abstract
Description
Claims
Application Information

- R&D Engineer
- R&D Manager
- IP Professional
- Industry Leading Data Capabilities
- Powerful AI technology
- Patent DNA Extraction
Browse by: Latest US Patents, China's latest patents, Technical Efficacy Thesaurus, Application Domain, Technology Topic, Popular Technical Reports.
© 2024 PatSnap. All rights reserved.Legal|Privacy policy|Modern Slavery Act Transparency Statement|Sitemap|About US| Contact US: help@patsnap.com