Self-adapting pipe robot
A pipe robot and self-adaptive technology, applied in the direction of special pipes, pipe components, mechanical equipment, etc., can solve the problems of high prices, no major breakthroughs in mechanical structures, and staying in the laboratory, etc., to achieve good bearing capacity, good self- The effect of adaptability and good stability
- Summary
- Abstract
- Description
- Claims
- Application Information
AI Technical Summary
Problems solved by technology
Method used
Image
Examples
Embodiment Construction
[0024] The technical scheme of the present invention is described in detail below in conjunction with accompanying drawing:
[0025] Such as figure 1 As shown, the present invention includes a fuselage 1; the outer circumference of the fuselage 1 is uniformly distributed at least three groups of driving devices 2 along the circumferential direction, and each group of driving devices 2 consists of four first connecting rods 21, four second connecting rods 22, one A sliding shaft 23, two sliding blocks 24, a fixing part 25, two pressure springs 26, two return springs 27, and four rollers 28 are formed. The sliding shaft 23 is arranged on the outer periphery of the fuselage 1, and the sliding shaft 23 The two ends are respectively connected with the fuselage 1, the fixing part 25 is welded in the middle of the sliding shaft 23, and the two sliders 24 are respectively sleeved on the sliding shaft 23 on both sides of the fixing part 25; two pressure springs 26 are respectively slee...
PUM
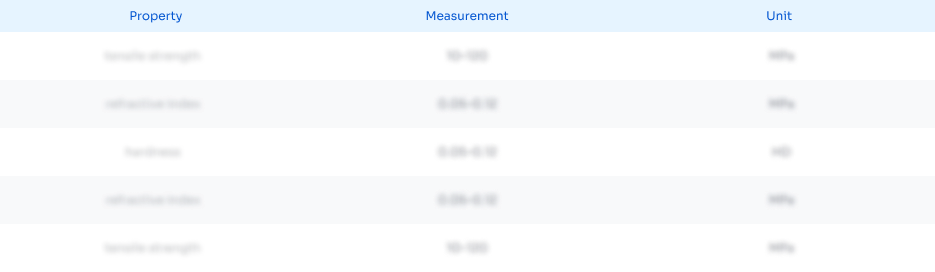
Abstract
Description
Claims
Application Information

- R&D Engineer
- R&D Manager
- IP Professional
- Industry Leading Data Capabilities
- Powerful AI technology
- Patent DNA Extraction
Browse by: Latest US Patents, China's latest patents, Technical Efficacy Thesaurus, Application Domain, Technology Topic, Popular Technical Reports.
© 2024 PatSnap. All rights reserved.Legal|Privacy policy|Modern Slavery Act Transparency Statement|Sitemap|About US| Contact US: help@patsnap.com