Thermal-insulation smelting composite furnace for non-ferrous metal
A thermal insulation composite, non-ferrous metal technology, applied in furnaces, crucible furnaces, furnace types, etc., to achieve convenient and effective use, solve the harsh production environment, and avoid the effects of easy evaporation
- Summary
- Abstract
- Description
- Claims
- Application Information
AI Technical Summary
Problems solved by technology
Method used
Image
Examples
Embodiment Construction
[0013] The present invention will be further described in detail below in conjunction with the accompanying drawings and embodiments.
[0014] Such as figure 1 As shown in FIG. 2 , the non-ferrous metal smelting and heat preservation composite furnace of this embodiment includes a smelting furnace 1 and a heat preservation furnace 3 , and a continuous casting crystallizer 4 is provided at the exit 32 of the heat preservation furnace 3 . A channel 31 is provided between the smelting furnace 1 and the holding furnace 3, and the channel 31 is a conduit 31a made of a material with good high temperature resistance. A control valve 2 is provided at the channel 31, and the valve 2 is an adjustable valve with adjustable flow rate. It includes a valve body 24 and a valve stem 22. The valve body 24 is placed horizontally on the bottom of the melting furnace 1. The upper side of the middle part of the body 24 is provided with an insertion cavity 25 into which the valve stem 22 can exten...
PUM
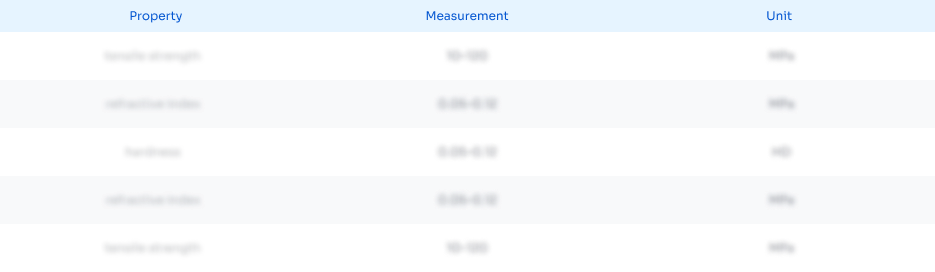
Abstract
Description
Claims
Application Information

- R&D
- Intellectual Property
- Life Sciences
- Materials
- Tech Scout
- Unparalleled Data Quality
- Higher Quality Content
- 60% Fewer Hallucinations
Browse by: Latest US Patents, China's latest patents, Technical Efficacy Thesaurus, Application Domain, Technology Topic, Popular Technical Reports.
© 2025 PatSnap. All rights reserved.Legal|Privacy policy|Modern Slavery Act Transparency Statement|Sitemap|About US| Contact US: help@patsnap.com