Method for self-spreading molten slag refounding CuCr alloy contact material
A technology of electroslag remelting and contact material, which is used in contacts, circuits, electrical switches, etc., can solve the problems of strict powder quality requirements, uncertain process parameters, and large fluctuations in oxygen content, so as to avoid macrosegregation. , reduce energy consumption, the effect of uniform composition
- Summary
- Abstract
- Description
- Claims
- Application Information
AI Technical Summary
Problems solved by technology
Method used
Examples
Embodiment 1
[0022] Take CuO, Cr 2 o 3 And Al powder by mass ratio CuO:Cr 2 o 3 : The ratio of Al powder is 100:114:160, that is to ensure that the excess of Al powder is 50%. 2 o 3 and Al powder) the percentage of total mass adds 5% CaF in the raw material 2, Mix the reactants evenly, then put the reaction mixture into the reaction furnace, add an appropriate amount of Mg powder on the surface of the reactants as an igniter to initiate the aluminothermic reduction reaction. At the same time, the electromagnetic stirring device is turned on, under the action of electromagnetic field stirring, the gold slag separation process is carried out to obtain a high-temperature copper-chromium alloy melt, and the circulating water is started for circulating water cooling, and the separated high-temperature alloy melt will be continuously cast into graphite In the casting mold, the preheating temperature of the graphite mold is 600°C. After stirring for 7 minutes, the stirring was stopped, and ...
Embodiment 2
[0024] Take CuO, Cr 2 o 3 And Al powder, by mass ratio CuO:Cr 2 o 3 : The ratio of Al powder is 100:110:150, that is, to ensure that the excess of Al powder is about 40%, and at the same time, add 2% NaF to the raw material, mix the reactants evenly, and then put the reaction mixture into the reaction furnace. An appropriate amount of Mg powder is added to the surface layer as an ignition agent to initiate the aluminothermic reduction reaction. At the same time, the electromagnetic stirring device is turned on, under the action of electromagnetic field stirring, the gold slag separation process is carried out to obtain a high-temperature copper-chromium alloy melt, and the circulating water is started for circulating water cooling, and the separated high-temperature alloy melt will be continuously cast into graphite In the casting mold, the preheating temperature of the graphite mold is 680°C. Continue to carry out electromagnetic stirring, and carry out circulating water ...
Embodiment 3
[0026] Take CuO, Cr 2 o 3 And Al powder, by mass ratio CuO:Cr 2 o 3 : The ratio of Al powder is 100:110:150, that is, to ensure that the Al powder is 40% excessive, and at the same time add 3% CaO to the raw material, mix the reactants evenly, and then put the reaction mixture into the reaction furnace. An appropriate amount of Mg powder is added as an igniter to initiate the aluminothermic reduction reaction. At the same time, the electromagnetic stirring device is turned on, under the action of electromagnetic field stirring, the gold slag separation process is carried out to obtain a high-temperature copper-chromium alloy melt, and the circulating water is started for circulating water cooling, and the separated high-temperature alloy melt will be continuously cast into graphite In the casting mold, the preheating temperature of the graphite mold is 700°C. Continue to carry out electromagnetic stirring, and carry out circulating water cooling at the same time. After sti...
PUM
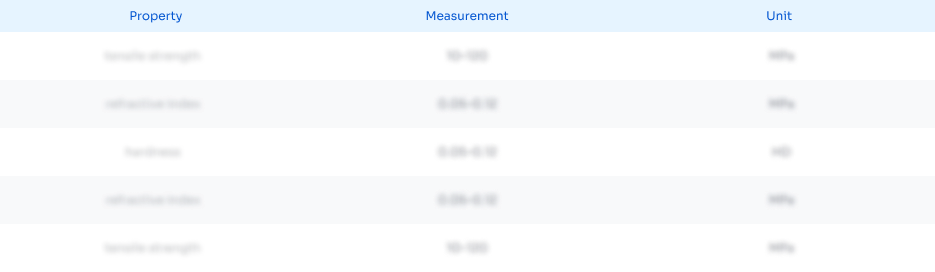
Abstract
Description
Claims
Application Information

- Generate Ideas
- Intellectual Property
- Life Sciences
- Materials
- Tech Scout
- Unparalleled Data Quality
- Higher Quality Content
- 60% Fewer Hallucinations
Browse by: Latest US Patents, China's latest patents, Technical Efficacy Thesaurus, Application Domain, Technology Topic, Popular Technical Reports.
© 2025 PatSnap. All rights reserved.Legal|Privacy policy|Modern Slavery Act Transparency Statement|Sitemap|About US| Contact US: help@patsnap.com