Optical scanning outside diameter measuring system without scanning objective lens and measuring method thereof
An optical scanning and measurement system technology, applied in the direction of measuring devices, optical devices, instruments, etc., can solve the problems of scanning objective lens design, manufacturing and assembly difficulties, restrictions on the promotion and use of equipment, and the difficulty of fully compensating errors, etc., to achieve the pupil position Reduced requirements, convenient debugging and maintenance, and improved reliability
- Summary
- Abstract
- Description
- Claims
- Application Information
AI Technical Summary
Problems solved by technology
Method used
Image
Examples
Embodiment Construction
[0026] The present invention will be described in further detail below in conjunction with the accompanying drawings and embodiments.
[0027] Such as figure 1 As shown, each unit is composed of a light source 1, a collimator mirror 2, a scanning mirror 3, a receiving objective lens 5, and a photoelectric receiver 6 connected to each other in sequence, and the photoelectric receiver 6 is also connected to a computer through a signal line. The light source (laser light source or LED light source) 1 is collimated by the collimator mirror 2 and projected on the scanning mirror 3 to form a scanning beam. The scanning beam scans the object 4 to form a scanning shadow, which is received by the subsequent photoelectric receiving lens 5 through the receiving objective lens 5. Receiver 6 receives, and processing circuit sends computer after signal processing, constitutes the basic unit of the present invention. The scanning mirror 3 has one or more reflective surfaces, the receiving o...
PUM
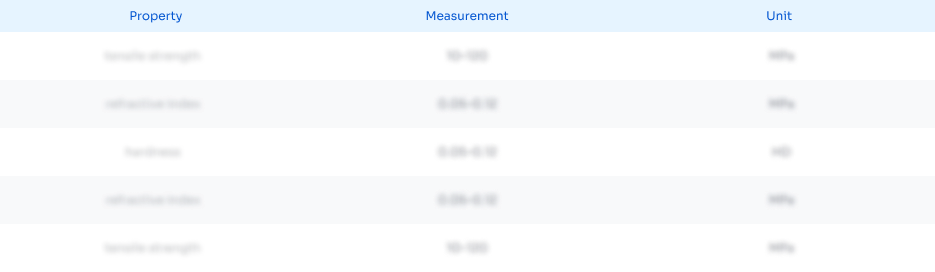
Abstract
Description
Claims
Application Information

- R&D
- Intellectual Property
- Life Sciences
- Materials
- Tech Scout
- Unparalleled Data Quality
- Higher Quality Content
- 60% Fewer Hallucinations
Browse by: Latest US Patents, China's latest patents, Technical Efficacy Thesaurus, Application Domain, Technology Topic, Popular Technical Reports.
© 2025 PatSnap. All rights reserved.Legal|Privacy policy|Modern Slavery Act Transparency Statement|Sitemap|About US| Contact US: help@patsnap.com