Radiation cooling method for power device of refrigeration device
A heat dissipation cooling and refrigeration device technology, which is applied in the cooling of instruments, parts of instruments, cooling/ventilation/heating transformation, etc., can solve problems such as poor heat transfer effect, unit failure, small heat transfer temperature difference, etc., and achieve improvement Reliability and cost reduction effects
- Summary
- Abstract
- Description
- Claims
- Application Information
AI Technical Summary
Problems solved by technology
Method used
Image
Examples
Embodiment Construction
[0011] Such as figure 1 As shown, the gas-liquid separator 2 in the low-temperature suction circuit part 1 of the compressor (the dotted line box part in the figure) has a plane 3 as an installation surface, and the power device 4 that needs to be dissipated in the electric control box of the refrigeration device is installed on the on that plane. Through the low-temperature refrigerant circulation in the gas-liquid separator, the heat transfer on this plane reduces the temperature of the device and realizes heat dissipation and cooling.
[0012] Such as figure 2 As shown, a metal heat-conducting installation surface 6 with good thermal conductivity is provided on the suction pipeline 5 in the low-temperature suction circuit part 1 of the compressor (the dotted line box part in the figure), and the metal heat-conducting mounting surface 6 with good thermal conductivity is arranged, and the cooling device electric control Power devices 4 are mounted on this face. Through th...
PUM
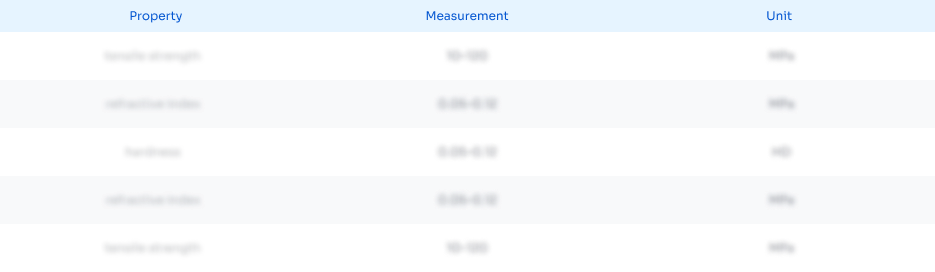
Abstract
Description
Claims
Application Information

- Generate Ideas
- Intellectual Property
- Life Sciences
- Materials
- Tech Scout
- Unparalleled Data Quality
- Higher Quality Content
- 60% Fewer Hallucinations
Browse by: Latest US Patents, China's latest patents, Technical Efficacy Thesaurus, Application Domain, Technology Topic, Popular Technical Reports.
© 2025 PatSnap. All rights reserved.Legal|Privacy policy|Modern Slavery Act Transparency Statement|Sitemap|About US| Contact US: help@patsnap.com