Composite thermal insulation concrete shear wall
A technology of concrete shear wall and thermal insulation concrete, applied in the direction of walls, building components, buildings, etc., can solve the problems of inability to satisfy comfort, poor overall performance, etc., and achieve the goal of improving thermal insulation efficiency, improving construction quality, and reducing cost. Effect
- Summary
- Abstract
- Description
- Claims
- Application Information
AI Technical Summary
Problems solved by technology
Method used
Image
Examples
Embodiment 1
[0028] see figure 1 , a composite thermal insulation concrete shear wall, including a wall 1 and a connecting beam 2, the wall 1 is composed of a prefabricated thermal insulation concrete wall 11 and a cast-in-place concrete wall 12, and the prefabricated thermal insulation concrete wall 11 is an inner surface cladding Concrete slab 5 with thermal insulation material layer 4, thermal insulation material layer 4 in prefabricated thermal insulation concrete wall 11 and cast-in-place concrete wall 12 are compositely poured into one body; It is integrated with the upper and lower cast-in-place concrete walls 12, and the outer end surface of the connecting beam 2 is covered with a layer of thermal insulation material 4.
[0029] see figure 2 , 3, 4, internal screw holes 16 are embedded at intervals in the prefabricated thermal insulation concrete wall 11, the screw 15 is inserted into the internal screw hole screw 16, and protrudes outside the insulation material layer 4 of the p...
PUM
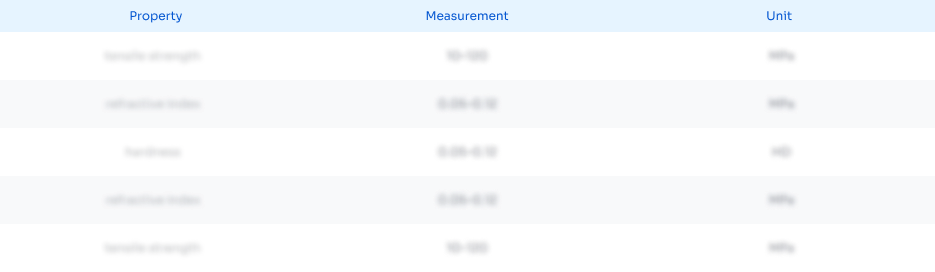
Abstract
Description
Claims
Application Information

- Generate Ideas
- Intellectual Property
- Life Sciences
- Materials
- Tech Scout
- Unparalleled Data Quality
- Higher Quality Content
- 60% Fewer Hallucinations
Browse by: Latest US Patents, China's latest patents, Technical Efficacy Thesaurus, Application Domain, Technology Topic, Popular Technical Reports.
© 2025 PatSnap. All rights reserved.Legal|Privacy policy|Modern Slavery Act Transparency Statement|Sitemap|About US| Contact US: help@patsnap.com