Differential piezoelectric three-dimensional force sensor
A sensor and three-dimensional force technology, applied in the measurement of the property force of the piezoelectric device, fluid pressure measurement using the piezoelectric device, etc., can solve the problems of insurmountable errors, weak output signals, and low measurement accuracy, and achieve structural Simple, strong output signal and high measurement accuracy
- Summary
- Abstract
- Description
- Claims
- Application Information
AI Technical Summary
Problems solved by technology
Method used
Image
Examples
Embodiment Construction
[0015] Differential piezoelectric three-dimensional force sensor (reference Figure 6 , 7 , 8, 9). Same as the prior art, the sensor includes a dynamometer composed of a quartz wafer with a signal output electrode and an insulating positioning frame for fixing the quartz wafer, with an inner cavity in which the dynamometer is packaged and a There is a base with a signal lead-out socket, and a cover that is pre-pressed on the quartz wafer and covers the base. Wherein, the signal output electrodes of the quartz wafer are connected with the signal lead-out sockets 12 on the base in one-to-one correspondence, and then directly connected with the differential charge amplifier by a commercially available connection line with a Teflon connector. The present invention is characterized in that the insulating positioning frame is provided with eight positioning holes, and the connecting lines between the centers of the positioning holes are square. Four positioning holes in them are ...
PUM
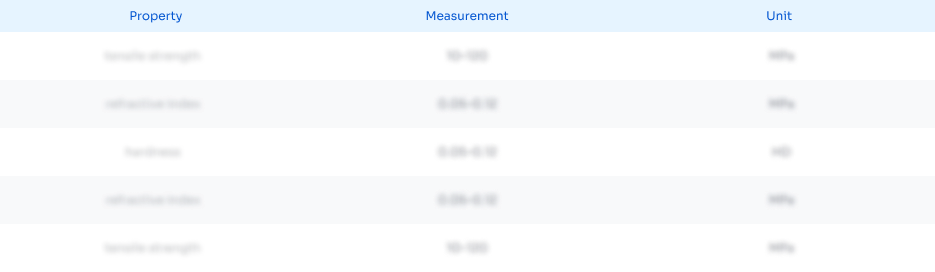
Abstract
Description
Claims
Application Information

- R&D
- Intellectual Property
- Life Sciences
- Materials
- Tech Scout
- Unparalleled Data Quality
- Higher Quality Content
- 60% Fewer Hallucinations
Browse by: Latest US Patents, China's latest patents, Technical Efficacy Thesaurus, Application Domain, Technology Topic, Popular Technical Reports.
© 2025 PatSnap. All rights reserved.Legal|Privacy policy|Modern Slavery Act Transparency Statement|Sitemap|About US| Contact US: help@patsnap.com