Synthesis method of nylon 6
A synthesis method and nylon technology, applied in the field of dehydration technology, can solve problems such as increasing production cost, and achieve the effect of reducing production cost
- Summary
- Abstract
- Description
- Claims
- Application Information
AI Technical Summary
Problems solved by technology
Method used
Examples
Embodiment 1
[0017] Solid adsorbent silica gel 500g, micropore diameter is 30 Molecular sieve 300g, pore diameter at 10
[0018] Silica gel directly at 250°C, N 2 Flow rate 12ml / min, activation time 3h, molecular sieve washing 3 times, N 2 The flow rate is 6ml / min, the temperature is 200°C, and the activation time is 3h. After melting 100 parts of caprolactam, pass through the refining column into the polymerization kettle, add 0.04 parts of potassium hydroxide at a temperature of 130±5°C, and vacuum dehydrate for 3 minutes under a residual pressure of 0.30 MPa. After eliminating the vacuum with dry nitrogen, add 0.04 parts of 2,4 Or 2,6 toluene diisocyanate (TDI) and 2.0 parts of polypropylene oxide, heated up to 180°C, and reacted for 15 minutes to obtain nylon 6 resin with a relative viscosity of 3.6. Its performance test indicators are shown in Table 1.
Embodiment 2
[0020] Solid adsorbent silica gel 400g, pore diameter at 40 Activated alumina 300g, micropore diameter at 15
[0021] Silica gel directly at 280°C, N 2 Flow rate 12ml / min, activation time 3h, activated alumina washed 3 times, N 2 The flow rate is 10ml / min, the temperature is 270°C, and the activation time is 3h. After melting 100 parts of caprolactam, pass through the refining column into the polymerization kettle, add 0.04 parts of sodium hydroxide at a temperature of 130±5°C, and vacuum dehydrate for 4 minutes under a residual pressure of 0.30 MPa. After the vacuum is eliminated with dry nitrogen, add 0.05 parts of 2,4 Or 2,6 toluene diisocyanate (TDI) and 1.0 part of polypropylene oxide, heated up to 170°C, and reacted for 20 minutes to obtain nylon 6 resin with a relative viscosity of 3.5. Its performance test indicators are shown in Table 1.
Embodiment 3
[0023] Solid adsorbent activated alumina 400g, micropore diameter at 20 Molecular sieve 300g, pore diameter at 10
[0024] Activated alumina washed 3 times at 270°C, N 2 Flow rate 9ml / min, activation time 3h, molecular sieve washing 3 times, N 2 The flow rate is 6ml / min, the temperature is 200°C, and the activation time is 3h. After melting 100 parts of caprolactam, pass through the refining column into the polymerization kettle, add 0.05 parts of potassium hydroxide at a temperature of 130±5°C, and vacuum dehydrate for 3 minutes under a residual pressure of 0.20 MPa. After the vacuum is eliminated with dry nitrogen, add 0.04 parts of 2,4 Or 2,6 toluene diisocyanate (TDI) and 1.5 parts of polypropylene oxide, heated up to 190°C, and reacted for 12 minutes to obtain a nylon 6 resin with a relative viscosity of 3.3. Its performance test indicators are shown in Table 1.
PUM
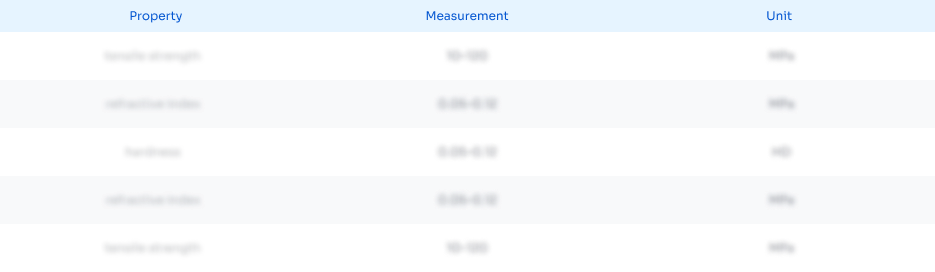
Abstract
Description
Claims
Application Information

- Generate Ideas
- Intellectual Property
- Life Sciences
- Materials
- Tech Scout
- Unparalleled Data Quality
- Higher Quality Content
- 60% Fewer Hallucinations
Browse by: Latest US Patents, China's latest patents, Technical Efficacy Thesaurus, Application Domain, Technology Topic, Popular Technical Reports.
© 2025 PatSnap. All rights reserved.Legal|Privacy policy|Modern Slavery Act Transparency Statement|Sitemap|About US| Contact US: help@patsnap.com