Method for preparing original medicne of 93% to 96% propargite
The technology of a special original drug, acetidine, is applied in the field of preparation of the original drug of acetidine with a content of 93% to 96%, which can solve the problems such as difficult removal of thionyl chloride, and achieve high content and high yield Effect
- Summary
- Abstract
- Description
- Claims
- Application Information
AI Technical Summary
Problems solved by technology
Method used
Image
Examples
Embodiment 1
[0039] (1) Preparation of p-tert-butylphenoxycyclohexanol: in a 100L reactor, add 15.3Kg p-tert-butylphenol (98%, 100mol), 10.9Kg epoxycyclohexane (99%, 110mol) , toluene 32.24L (99%, 300mol), reacted at 120°C for 12 hours, washed three times, each time with 20Kg of hot water at a temperature of 70°C to 80°C; at a pressure of 15mmHg and a temperature of 115°C, vacuum distillation Excess epoxycyclohexane and toluene were removed in 2.5 hours to obtain 22.89 Kg of white p-tert-butylphenoxycyclohexanol, that is, the content of the first intermediate was 98.5%, and the yield was 99.0%.
[0040] (2) Preparation of 2-(4-tert-butyl) cyclohexyl chlorosulfite toluene solution: in a 50L reactor, 11.76Kg p-tert-butylphenoxycyclohexanol (98.5%, 50mol) was dissolved in 15L In toluene, when the temperature was lowered to 40° C., 5.95 Kg of thionyl chloride (99%, 50 mol) was added dropwise, and the mixture was kept at 35° C. for 15 hours. After the heat preservation is completed, add 1.81L ...
Embodiment 2
[0044](1) Preparation of p-tert-butylphenoxycyclohexanol: in a 100L reactor, add 15.3Kg p-tert-butylphenol (98%, 100mol), 10.9Kg epoxycyclohexane (99%, 110mol) , toluene 32.24L (99%, 300mol), reacted at 120°C for 12 hours, washed three times, each time with a temperature of 80°C hot water 20Kg; at a pressure of 25mmHg, a temperature of 120°C, decompression distillation for 3 hours Excessive epoxy cyclohexane and toluene were removed to obtain 22.89 Kg of white p-tert-butylphenoxycyclohexanol, that is, the content of the first intermediate was 98.5%, and the yield was 98.5%.
[0045] (2) Preparation of 2-(4-tert-butyl) cyclohexyl chlorosulfite toluene solution: in a 50L reactor, 11.76Kg p-tert-butylphenoxycyclohexanol (98.5%, 50mol) was dissolved in 15L In toluene, when the temperature was lowered to 40°C, 7.14Kg of thionyl chloride (99%, 60mol) was added dropwise, and the mixture was kept at 38°C for 13 hours. After the heat preservation is completed, 4.36L of dichloromethane...
Embodiment 3
[0049] Repeat the same steps as described in Example 1, but from step (2): the preparation of 2-(4-tert-butyl)cyclohexyl chlorosulfite toluene solution: in a 50L reactor, 11.76Kg Tert-butylphenoxycyclohexanol (98.5%, 50mol) was dissolved in 15L of toluene, and when the temperature was lowered to 40°C, 7.14Kg of thionyl chloride (99%, 60mol) was added dropwise, and kept at 38°C for 15 hours. After the heat preservation is completed, add 6.54L dichloroethane to the reaction kettle, and at 38°C, the pressure is 25mmHg, and the vacuum distillation is carried out for 4 hours to remove the excess thionyl chloride to obtain 2-(4-tert-butyl) The toluene solution of cyclohexyl chlorosulfite, that is, 48.5 mol of the second intermediate, has a yield of 97%.
[0050] The second intermediate is condensed with propynyl alcohol to obtain 93.6% of propargite content and 92.3% of propargite yield.
[0051] All the other are with embodiment 1.
PUM
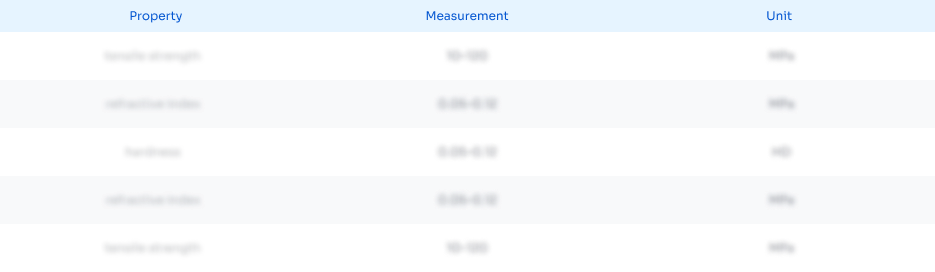
Abstract
Description
Claims
Application Information

- Generate Ideas
- Intellectual Property
- Life Sciences
- Materials
- Tech Scout
- Unparalleled Data Quality
- Higher Quality Content
- 60% Fewer Hallucinations
Browse by: Latest US Patents, China's latest patents, Technical Efficacy Thesaurus, Application Domain, Technology Topic, Popular Technical Reports.
© 2025 PatSnap. All rights reserved.Legal|Privacy policy|Modern Slavery Act Transparency Statement|Sitemap|About US| Contact US: help@patsnap.com