Controlling device of permanent-magnet synchro motor
A technology of permanent magnet synchronous and control device, applied in starting device, single motor speed/torque control, current controller, etc., can solve the problem of insufficient torque and torque, high price of absolute position detector, electrical phase angle correction Big problems and other problems, to achieve the effect of fast and smooth start
- Summary
- Abstract
- Description
- Claims
- Application Information
AI Technical Summary
Problems solved by technology
Method used
Image
Examples
Embodiment approach 1
[0024] FIG. 1 is a configuration diagram of a control device for a permanent magnet synchronous motor according to Embodiment 1 of the present invention. The control device of this permanent magnet synchronous motor is constituted as a speed control system 100 (equivalent to the d-q axis non-interference control system 101 (corresponding to the part shown by the dashed line in FIG. 1 ) generally used as a current control system (corresponding to the The part shown by the single dotted line) is further added with a detection mode setting unit 18, a magnetic pole detection current command unit 19, a magnetic pole phase determination unit 20, and switches 21a to 21c.
[0025] First, the configuration of the speed control system 100 will be described. The d-q axis non-interference control system is conventional, and is used to control the current of the permanent magnet synchronous motor 1, and is a general control method that also includes speed control. The speed control system...
Embodiment approach 2
[0073] In Embodiment 1, the case where the d-axis current command value Idph is increased has been described as a method for easily generating the hunting phenomenon. In Embodiment 2, another method that is likely to cause a hunting phenomenon will be described.
[0074] As shown in the Bode diagram of FIG. 4 , the oscillation phenomenon can also be easily generated by delaying the phase in the high-frequency region. Therefore, in the process of step S512 in FIG. 5 , a delay element (redundant time element) may be inserted into the current control loop instead of increasing the d-axis current command value Idph.
[0075] 7 is a block diagram showing a d-axis current control system including a delay element 23 and a switch 24 according to Embodiment 2 of the present invention. The delay element 23 outputs the feedback current value Id' having a time delay with respect to the feedback current value Id of the current control system. In addition, the switch 24 is a second signal...
PUM
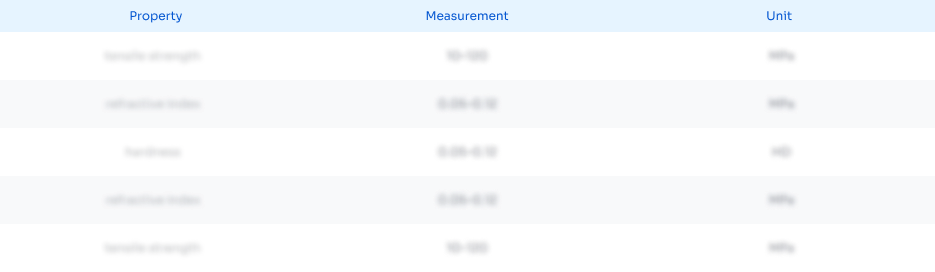
Abstract
Description
Claims
Application Information

- Generate Ideas
- Intellectual Property
- Life Sciences
- Materials
- Tech Scout
- Unparalleled Data Quality
- Higher Quality Content
- 60% Fewer Hallucinations
Browse by: Latest US Patents, China's latest patents, Technical Efficacy Thesaurus, Application Domain, Technology Topic, Popular Technical Reports.
© 2025 PatSnap. All rights reserved.Legal|Privacy policy|Modern Slavery Act Transparency Statement|Sitemap|About US| Contact US: help@patsnap.com