Plastic filtering board or board forming process
A molding method and filter plate technology, which are used in household components, household appliances, other household appliances, etc., can solve the problems of filter plate strength and quality, unsatisfactory insulation effect of material barrels, and long moving process of material barrels. , to achieve the effect of shortening material consumption, good thermal insulation effect, and reducing the types of formulas
- Summary
- Abstract
- Description
- Claims
- Application Information
AI Technical Summary
Problems solved by technology
Method used
Image
Examples
Embodiment 1
[0010] Embodiment 1: with reference to accompanying drawing 1. Plastic filter plate forming method, the hot runner port of the hot runner plastic filter plate forming mold or the hot runner plate forming mold is located on the upper part or the bottom or the side of the hot runner plastic filter plate forming mold or the hot runner plate forming mold, the injection molding mechanism of the injection molding machine The discharge port is aligned with the hot runner port. After the plastic raw material is heated and plasticized by the injection molding mechanism, the discharge port is injected into the cavity of the mold through the hot runner in the hot runner plastic filter plate forming mold or the hot runner plate forming mold, and then cooled and finalized. After the mold is opened, the filter plate or plate can be taken out. When the hot runner opening of the hot runner plastic filter plate forming mold or the hot runner plate forming mold is located on the upper part of t...
Embodiment 2
[0011] Embodiment 2: plastic filter plate forming method, the hot runner port of the hot runner plastic filter plate forming mold or the hot runner plate forming mold is located at the top or bottom or side of the hot runner plastic filter plate forming mold or the hot runner plate forming mold, and the injection molding mechanism The outlet of the outlet is aligned with the hot runner mouth, the hydraulic press is closed, the plastic raw material is heated and plasticized by the injection molding mechanism, and the outlet is injected into the cavity of the mold through the hot runner in the hot runner plastic filter plate forming mold or the hot runner plate forming mold After internal forming, cooling and setting, the hydraulic press opens the mold to take out the filter plate or plate. The filter plate or plate forming mold is located in the hydraulic press and is clamped and opened by the hydraulic press. The hot runner device is located on the upper or bottom or side of th...
PUM
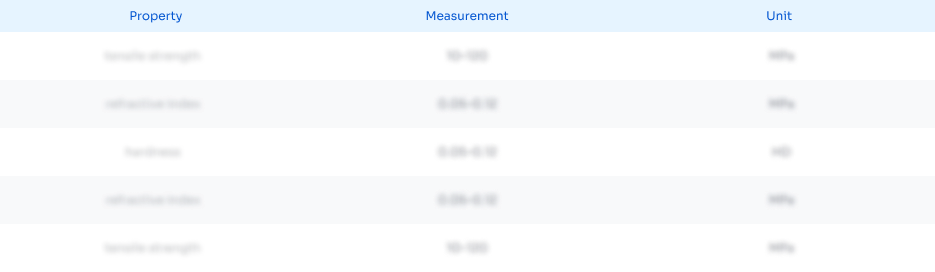
Abstract
Description
Claims
Application Information

- R&D
- Intellectual Property
- Life Sciences
- Materials
- Tech Scout
- Unparalleled Data Quality
- Higher Quality Content
- 60% Fewer Hallucinations
Browse by: Latest US Patents, China's latest patents, Technical Efficacy Thesaurus, Application Domain, Technology Topic, Popular Technical Reports.
© 2025 PatSnap. All rights reserved.Legal|Privacy policy|Modern Slavery Act Transparency Statement|Sitemap|About US| Contact US: help@patsnap.com