Method and apparatus for measuring distance and direction by movable magnetic field source
- Summary
- Abstract
- Description
- Claims
- Application Information
AI Technical Summary
Benefits of technology
Problems solved by technology
Method used
Image
Examples
second embodiment
the present invention is illustrated diagrammatically in FIG. 5, in which a generally horizontal well 80 has a vertical portion 82 and a generally horizontal portion 84. The vertical depth of the well may be in the range of 1,500 meters, for example, while the horizontal portion 84 may extend a thousand meters or more. As has been described above, the horizontal well may be of the type used in the petroleum industry in an oil producing sand where it is desired to drill parallel horizontal wells for use in steam assisted recovery projects. Accordingly, as illustrated, a second borehole 85 including an upper, vertical portion 88 and a lower, horizontal 90 is drilled in a controlled trajectory so that its horizontal portion 90 is less than about 20 meters from the horizontal portion 84 of well 80 and is maintained generally parallel to the existing well during drilling. Preferably, the horizontal portion 90 is drilled on a course which is separated by 10 meters, .+-.1 meter, and is dir...
PUM
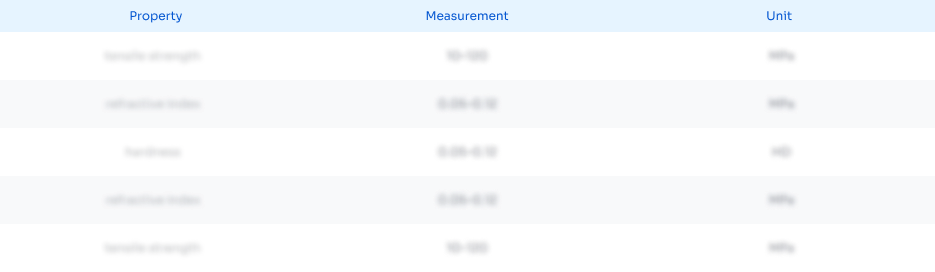
Abstract
Description
Claims
Application Information

- R&D
- Intellectual Property
- Life Sciences
- Materials
- Tech Scout
- Unparalleled Data Quality
- Higher Quality Content
- 60% Fewer Hallucinations
Browse by: Latest US Patents, China's latest patents, Technical Efficacy Thesaurus, Application Domain, Technology Topic, Popular Technical Reports.
© 2025 PatSnap. All rights reserved.Legal|Privacy policy|Modern Slavery Act Transparency Statement|Sitemap|About US| Contact US: help@patsnap.com