Liquid discharge device and liquid discharge method
- Summary
- Abstract
- Description
- Claims
- Application Information
AI Technical Summary
Benefits of technology
Problems solved by technology
Method used
Image
Examples
first embodiment
[0066]Description will be made regarding a first embodiment of the present invention with reference to the drawings and the like. The first embodiment has been made generally in order to achieve the first object of the present invention. Note that the term “ink droplet” used here means a small amount (e.g., several picoliters) of ink (liquid) discharged from a nozzle 18 of a liquid discharge portion described later. Also, the term “dot” used here means a dot formed of one ink droplet discharged on a recording medium such as a printing paper sheet or the like. Also, the term “pixel” used here is the smallest increment of an image, and the term “pixel region” used here means a region for forming the pixels.
[0067]In general, a predetermined number of liquid droplets (0, 1, or more) are discharged onto each pixel region, whereby a pixel with a predetermined tone level (tone level, 1, 2, 3, or more) is formed on each pixel region. That is to say, one pixel region has zero, one, or more d...
second embodiment
[0217]Next, a second embodiment according to the present invention will be described. Note that description of the same configuration as with the first embodiment will be omitted.
[0218]It is a principal object of the present second embodiment to provide an arrangement wherein occurrence of defects in the image due to malfunctioning of the head, such as occurrence of streaks between the pixel columns or the like is suppressed, even in the event that malfunctioning such as non-discharge occurs in a part of the liquid discharge portions.
[0219]Furthermore, it is another object (secondary object) thereof to provide an arrangement wherein the irregularities in an array of landing positions of the liquid droplets are less conspicuous.
[0220]Accordingly, the arrangement according to the present embodiment includes the head 11 employing the discharge direction varying means described in the first embodiment, first discharge control means, second discharge control means, and third discharge co...
PUM
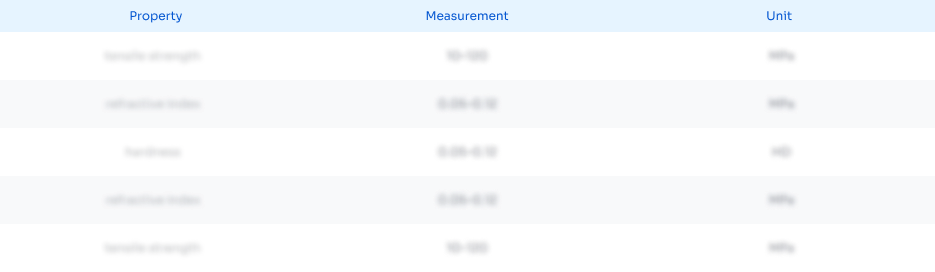
Abstract
Description
Claims
Application Information

- R&D
- Intellectual Property
- Life Sciences
- Materials
- Tech Scout
- Unparalleled Data Quality
- Higher Quality Content
- 60% Fewer Hallucinations
Browse by: Latest US Patents, China's latest patents, Technical Efficacy Thesaurus, Application Domain, Technology Topic, Popular Technical Reports.
© 2025 PatSnap. All rights reserved.Legal|Privacy policy|Modern Slavery Act Transparency Statement|Sitemap|About US| Contact US: help@patsnap.com