Thermal energy recovery device
a technology of energy recovery device and thermal energy, which is applied in the direction of safety/regulation device, machine/engine, steam engine plant, etc., can solve the problems of poor lubrication of bearings, reduced rotational speed of the pump, and insufficient lubrication of the bearings of the screw turbine when the device restarts
- Summary
- Abstract
- Description
- Claims
- Application Information
AI Technical Summary
Benefits of technology
Problems solved by technology
Method used
Image
Examples
first embodiment
[0024]FIG. 1 shows the configuration of a thermal energy recovery device according to a first embodiment of the present invention. The thermal energy recovery device includes an evaporator 10, an expander 20, a power recovery machine 30, a condenser 40, a pump 50, a circulation flow path 60 connecting the evaporator 10, the expander 20, the condenser 40, and the pump 50 in this order, a cooling flow path 70, and a control unit 80.
[0025]The evaporator 10 evaporates working medium through heat exchange between the working medium and heating medium.
[0026]The expander 20 is provided at a site downstream the evaporator 10 in the circulation flow path 60. The expander 20 expands working medium of gas phase flowing out of the evaporator 10. In this embodiment, the expander 20 employs a volumetric screw expander having a rotor to be rotationally driven by the expansion energy of working medium of gas phase. Specifically, the expander 20 has a pair of male and female screw rotors (rotors) 21...
second embodiment
[0045]Next will be described a thermal energy recovery device according to a second embodiment of the present invention with reference to FIG. 3. It is noted that in the second embodiment, only components different from the first embodiment will be described, and the same structures, operations, and effects as in the first embodiment will not be described.
[0046]In this embodiment, the power recovery machine 30 has a jacket 36, and the downstream end portion of the cooling flow path 70 is connected to the jacket 36.
[0047]The jacket 36 provided in the secondary casing 35 to form a cooling space S that allows working medium of liquid phase to flow between the jacket 36 and the secondary casing 35. The jacket 36 is arranged on the outside of the outer peripheral surface of the secondary casing 35. That is, the cooling space S is formed between the outer peripheral surface of the secondary casing 35 and the inner peripheral surface of the jacket 36. The jacket 36 has an introducing porti...
third embodiment
[0050]Next will be described a thermal energy recovery device according to a third embodiment of the present invention with reference to FIG. 4. It is noted that in the third embodiment, only components different from the first embodiment will be described, and the same structures, operations, and effects as in the first embodiment will not be described.
[0051]While this embodiment shares similarity with the second embodiment in that the power recovery machine 30 has a jacket 36, cooling medium (e.g. cooling water) different from the working medium is supplied to the cooling space S.
[0052]A cooling flow path 73 branched from a cooling medium supply line L1 for supplying cooling medium therethrough is connected to the jacket 36. Accordingly, in this embodiment, cooling medium passing through the cooling space S cools the power recovery unit 31 via the secondary casing 35. Cooling medium that has passed through the cooling space S is returned through a cooling medium recovery flow path...
PUM
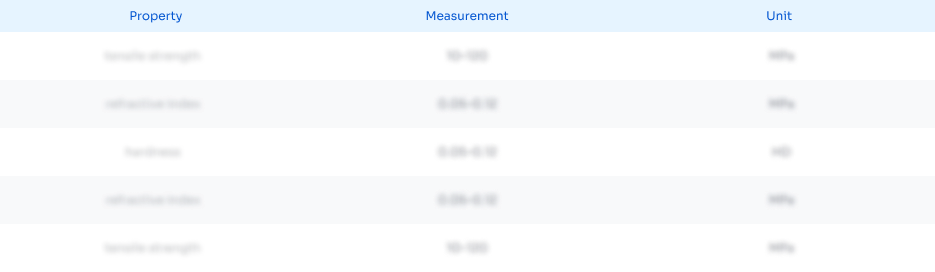
Abstract
Description
Claims
Application Information

- R&D
- Intellectual Property
- Life Sciences
- Materials
- Tech Scout
- Unparalleled Data Quality
- Higher Quality Content
- 60% Fewer Hallucinations
Browse by: Latest US Patents, China's latest patents, Technical Efficacy Thesaurus, Application Domain, Technology Topic, Popular Technical Reports.
© 2025 PatSnap. All rights reserved.Legal|Privacy policy|Modern Slavery Act Transparency Statement|Sitemap|About US| Contact US: help@patsnap.com