Realtime payload mapping for loader/hauler system optimization
a real-time payload mapping and loader/hauler technology, applied in soil shifting machines/dredgers, construction, etc., can solve the problems of operator difficulty in properly balancing each load, operator may not be able to properly view the previously placed loads, operator may be unable to pick out the best place,
- Summary
- Abstract
- Description
- Claims
- Application Information
AI Technical Summary
Benefits of technology
Problems solved by technology
Method used
Image
Examples
Embodiment Construction
[0019]Referring now to the drawings and with specific reference to FIG. 1, a jobsite 20 with a set of work machines 22 is shown, in accordance with certain embodiments of the present disclosure. While one non-limiting example of the set of work machines 22 may include a hauling machine 24 and a loading machine 26, it will be understood that the set of work machines 22 may include other types of machines such as but not limited to, an on-road truck, an off-road truck, a motor grader, industrial mining equipment, a locomotive, and any other such machines. The hauling machine 24 may include a frame 28 configured to support a power source 30, and an operator compartment or operator cabin 32. In some embodiments, the power source 30 may be a power generating source such as but not limited to, a diesel combustion engine, a gasoline combustion engine, a generator, an electric motor, any other known power generating source or a combination thereof. Moreover, the operator compartment 32 may ...
PUM
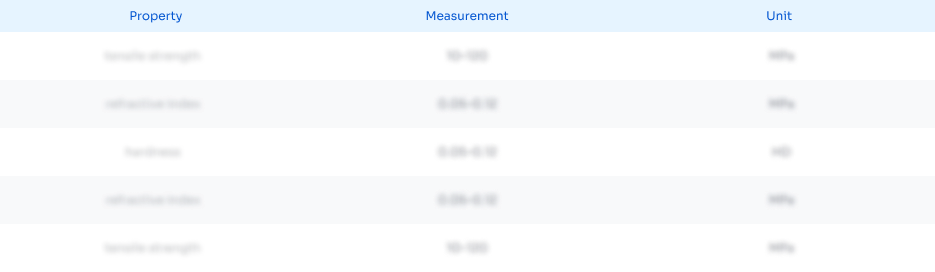
Abstract
Description
Claims
Application Information

- R&D
- Intellectual Property
- Life Sciences
- Materials
- Tech Scout
- Unparalleled Data Quality
- Higher Quality Content
- 60% Fewer Hallucinations
Browse by: Latest US Patents, China's latest patents, Technical Efficacy Thesaurus, Application Domain, Technology Topic, Popular Technical Reports.
© 2025 PatSnap. All rights reserved.Legal|Privacy policy|Modern Slavery Act Transparency Statement|Sitemap|About US| Contact US: help@patsnap.com