Wellbore encasement
a wellbore and wellbore technology, applied in the field of wellbore encasement, can solve the problems of gas bubbles entering cement, horizon catastrophe, and catastrophe, and achieve the effect of less rotation and faster material deposition
- Summary
- Abstract
- Description
- Claims
- Application Information
AI Technical Summary
Benefits of technology
Problems solved by technology
Method used
Image
Examples
Embodiment Construction
[0060]In simple terms, the invention relates to the concept of depositing lining material to wellbores using 3D printing technology. A media dispensing apparatus including at least one nozzle is inserted down a borehole for depositing multiple layers of lining material to the interior surface of the borehole in a controlled manner. One embodiment is shown in FIGS. 5 and 8, in which the nozzle is mounted via a universal joint to a distal end of a hollow support rod. The support rod contains a primary flexible conduit for fluidly connecting the nozzle with a source of a first lining material. The support rod further contains a secondary flexible conduit for fluidly connecting the nozzle with a source of a second lining material, different to the first. As shown in FIG. 6, the nozzle and the conduits may be arranged to dispense the first and second materials simultaneously, in a form of extrusion. In other embodiments, only a single source of material is connected to the nozzle.
[0061]I...
PUM
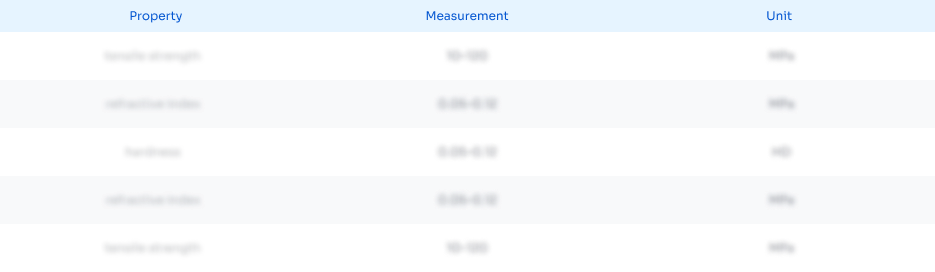
Abstract
Description
Claims
Application Information

- R&D
- Intellectual Property
- Life Sciences
- Materials
- Tech Scout
- Unparalleled Data Quality
- Higher Quality Content
- 60% Fewer Hallucinations
Browse by: Latest US Patents, China's latest patents, Technical Efficacy Thesaurus, Application Domain, Technology Topic, Popular Technical Reports.
© 2025 PatSnap. All rights reserved.Legal|Privacy policy|Modern Slavery Act Transparency Statement|Sitemap|About US| Contact US: help@patsnap.com