Ganged single axis solar tracker and its drive system
a solar tracker and drive system technology, applied in solar heat systems, solar thermal energy generation, lighting and heating apparatus, etc., can solve the problems of limiting the total area of solar tracker arrays driven by each motor/driver, high cost of solar tracker array using this technology, and high cos
- Summary
- Abstract
- Description
- Claims
- Application Information
AI Technical Summary
Benefits of technology
Problems solved by technology
Method used
Image
Examples
third embodiment
[0035]this invention is shown in FIG. 7. In this example, the drive axis is located near the center of the tracker array while it is apart from any tracker rotation axis.
fourth embodiment
[0036]In this invention as shown in FIG. 8, the drive axis is located on one side of and apart from the tracker array.
[0037]In any particular applications of the present invention, solar receivers can all have the same or various initial tracker angles; the tracker rotation beam can be of round or square cross section, a truss or any other composite structure.
[0038]In all embodiments as shown the tracker axes are flat. It is not difficult to persons skilled in the art that the tracker axes can be aligned tilted to the ground or vertical.
[0039]The term “ground” as used in reference to the foundation is not limited to earth or soils, but can be a rooftop or any other supporting structures.
PUM
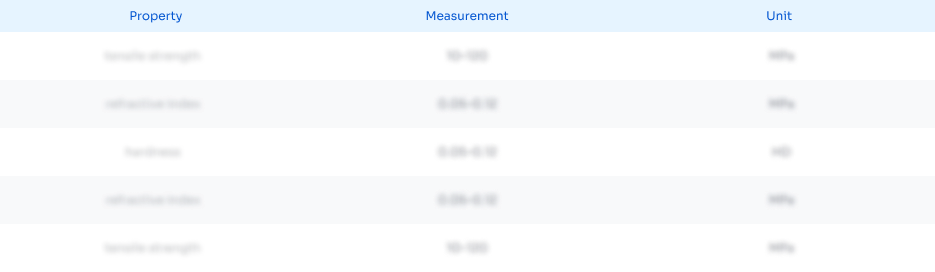
Abstract
Description
Claims
Application Information

- R&D
- Intellectual Property
- Life Sciences
- Materials
- Tech Scout
- Unparalleled Data Quality
- Higher Quality Content
- 60% Fewer Hallucinations
Browse by: Latest US Patents, China's latest patents, Technical Efficacy Thesaurus, Application Domain, Technology Topic, Popular Technical Reports.
© 2025 PatSnap. All rights reserved.Legal|Privacy policy|Modern Slavery Act Transparency Statement|Sitemap|About US| Contact US: help@patsnap.com