Sliding Bearing and Pump Device Using the Same
a technology of sliding bearing and pump device, which is applied in the direction of mechanical equipment, machines/engines, liquid fuel engines, etc., can solve the problems of limited fluid that can be used for the lubrication of sliding bearings, the sliding bearing itself which is used in the pump device is subject to conditions where it is difficult to obtain high dynamic pressure, and it is difficult for the structure to increase the load carrying capacity without. , the loading capacity and the rigidity of the entire sliding bearing can be increased, and the effect o
- Summary
- Abstract
- Description
- Claims
- Application Information
AI Technical Summary
Benefits of technology
Problems solved by technology
Method used
Image
Examples
embodiment 1
[0049]An embodiment 1 of the present invention will be explained with reference to a vertical-type pump device 100 having a journal bearing-type sliding bearing according to the present invention incorporated therein.
[0050]FIG. 1 is a structure view of the vertical-type pump device 100 according to this embodiment. A passage 104 which communicates between an inlet port 102 and an outlet port 103 is formed in the interior of a casing 101. At the midway of the passage 104, an impeller 105 is provided at a tip end of a shaft 106 connected to an external rotation power source 107.
[0051]The shaft 106 is rotatably supported, on a side thereof adjacent to the rotation power source 107, by a bearing 108, and is rotatably supported, on a side thereof adjacent the impeller 105, by a sliding bearing 109. Supply of power from the rotation power source 107 causes the shaft 106 to be rotated to rotation-move the impeller 105, whereby fluid such as fluid metal which flows into an interior of the p...
embodiment 2
[0062]The main purpose of providing the hydrostatic pressure pocket rows adjacently to the both end portions of the inner periphery of the sleeve lies in that pressure at the both ends of the circular cylindrical inner peripheral surface region arranged so as to be interposed between the hydrostatic pressure pocket rows is kept in a high state and a level of the dynamic pressure produced on the circular cylindrical inner peripheral surface region is kept.
[0063]FIG. 6 shows an embodiment 2 of a sleeve portion of a sliding bearing that more positively attains this purpose. Two hydrostatic pressure pocket rows 116 are arranged adjacently to each of the both end portions of the inner periphery of a sleeve 111B. In the two adjacent hydrostatic pressure pocket rows 116, hydrostatic pressure pockets 112B are arranged so as to be staggered in the circumferential direction.
[0064]A circular cylindrical inner peripheral surface region 115 in which the hydrostatic pressure pockets 112B are not ...
embodiment 3
[0066]FIG. 7 shows an embodiment 3 of a sleeve portion of a sliding bearing which increases pressure on neighborhoods of the both end portions of a sleeve 111C, i.e., the both ends of the circular cylindrical inner peripheral surface region 115. Hydrostatic pressure pockets 112C have shapes asymmetrical in the circumferential direction and in the axial direction of the shaft 106. Hydrostatic pressure pocket-extending portions 117 are partially provided at the both ends of the hydrostatic pressure pockets 112C in the circumferential direction. Hydrostatic pressure pocket-extending portions 117 of a hydrostatic pressure pocket 112C are separated from hydrostatic pressure pocket-extending portions 117 of a circumferentially adjacent hydrostatic pressure pocket 112C but are partially superposed on them within a fixed circumferential arrangement-angle range.
[0067]Each hydrostatic pressure pocket 112C is formed with a hydrostatic pressure pocket-extending portion 117 extending to the upst...
PUM
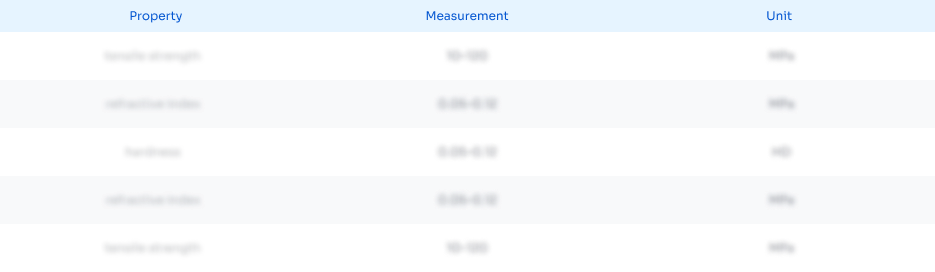
Abstract
Description
Claims
Application Information

- R&D
- Intellectual Property
- Life Sciences
- Materials
- Tech Scout
- Unparalleled Data Quality
- Higher Quality Content
- 60% Fewer Hallucinations
Browse by: Latest US Patents, China's latest patents, Technical Efficacy Thesaurus, Application Domain, Technology Topic, Popular Technical Reports.
© 2025 PatSnap. All rights reserved.Legal|Privacy policy|Modern Slavery Act Transparency Statement|Sitemap|About US| Contact US: help@patsnap.com