Burner assembly
a technology of burners and components, applied in the direction of burners, hot gas positive displacement engine plants, combustion processes, etc., can solve the problems of small drop formation and less effective penetration, and achieve the effect of narrowing the radial fuel profil
- Summary
- Abstract
- Description
- Claims
- Application Information
AI Technical Summary
Benefits of technology
Problems solved by technology
Method used
Image
Examples
Embodiment Construction
[0088]FIG. 1 shows a detail of an inventive burner assembly in the region of a main burner 107. Swirl blades 17 are arranged around the lance in the housing 12 of the main burner 107. The swirl blades 17 are arranged along the periphery of the lance in the housing 12. The swirl blades 17 direct a compressor air flow 15 into the part of the burner 107 leading to a combustor. The air is made to swirl by the swirl blades 17. The lance also comprises a fuel channel 16. The burner 107 further comprises an attachment 13 on the side leading to a combustor. The attachment 13 can be welded or screwed to the lance for example. The fuel nozzles are preferably arranged downstream of the swirl blades 17 in the attachment 13 and are thus connected for flow purposes to the fuel channel 16, shown here as an oil channel. The inventive burner assembly preferably comprises eight such main burners 107 arranged in a circle (see FIG. 12). The main burners 107 here are arranged around a pilot burner (see ...
PUM
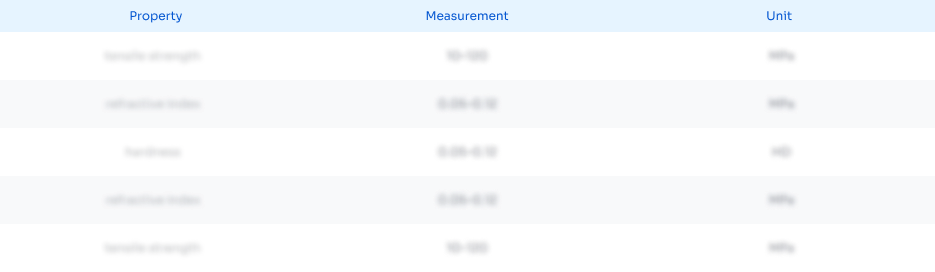
Abstract
Description
Claims
Application Information

- R&D
- Intellectual Property
- Life Sciences
- Materials
- Tech Scout
- Unparalleled Data Quality
- Higher Quality Content
- 60% Fewer Hallucinations
Browse by: Latest US Patents, China's latest patents, Technical Efficacy Thesaurus, Application Domain, Technology Topic, Popular Technical Reports.
© 2025 PatSnap. All rights reserved.Legal|Privacy policy|Modern Slavery Act Transparency Statement|Sitemap|About US| Contact US: help@patsnap.com