Control device with thumb trigger
a control device and thumb trigger technology, applied in the direction of cycle control systems, cycle equipment, instruments, etc., can solve the problems of manual control that has to be actuated, control of a system that requires a rapid reaction, and the difficulty of vigorous grasping of the handle of the machine, so as to achieve optimal grip
- Summary
- Abstract
- Description
- Claims
- Application Information
AI Technical Summary
Benefits of technology
Problems solved by technology
Method used
Image
Examples
first embodiment
[0075]In all the figures, the references bearing the same numbers relate to corresponding elements having similar functions. As illustrated in FIGS. 1 to 5, the device comprises a handle 10, grasped by a hand 1 and clutched by the index finger 6, the middle finger 7, the ring finger 8 and the little finger 9. The thumb 2 is for its part placed under the handle 10, its proximal phalanx 3 resting on the latter, thereby gripping it. The handle 10 is fixed to a handle support 11. The handle support 11 may be a handlebar or a steering wheel.
[0076]A trigger support 12 is fixed to the handle support 11 thanks to two screws 29. A trigger 13 can be moved on the trigger support 12 by articulating about a virtual axis 16 close to the articulation of the thumb 5. This trigger 13 is furnished with attachments 21 onto one of which a connecting part 20 is attached. A cable 24 allowing the operation of a controlled system is fixed to this connecting part 20 and slides in a sleeve 22, attached to th...
second embodiment
[0102]With the aid of FIGS. 8 to 10, the second embodiment will now be described. A trigger 50 is attached to the trigger support 12 and can be moved in rotation about an axis 51.
[0103]As illustrated in FIGS. 9 and 10, the axis of rotation 51 is no longer close to the normal 45 to the reference plane 18 as in the first embodiment, but substantially parallel to the latter. A return system 28 allows the trigger 13 to return to a rest position.
[0104]The return means 28 comprises a spring bearing on a protrusion 52 at a point distant from the axis of rotation 51. A connecting part 53 connects the protrusion 52 to a piston 30 which, during a travel 19, will generate a pressure in order to operate the controlled system. The proximal phalanx / distal phalanx reference plane 18 is in this instance substantially parallel to the axis 15 of the handle.
[0105]It is also possible to use another type of return system, such as for example a hydraulic or pneumatic system which does not necessarily use...
third embodiment
[0107]In the third embodiment, illustrated in FIG. 11, a trigger 60 moves in translation relative to the trigger support 12 thanks to two guides 35. The end 14 of the trigger moves parallel to the axis 15 of the handle 10.
[0108]Because of the sliding of the lateral side 44 of the proximal phalanx 3 along a bearing surface 46 of the handle 10, the internal face of the end of the distal phalanx follows the movement of the end 14 of the trigger 13 with a reduced relative sliding action. A return spring 61 is attached between the trigger 60 and the trigger support 12.
[0109]A linear position sensor 62 without contact is attached to the trigger support 12 and informs a real time system on the position of the trigger 13 so that the latter operates the controlled system.
[0110]In a variant, the movement of the trigger may very well be a combination of a rotation about an axis and a translation, described above, in order to best adapt to the preferences of the user.
[0111]The fourth embodiment...
PUM
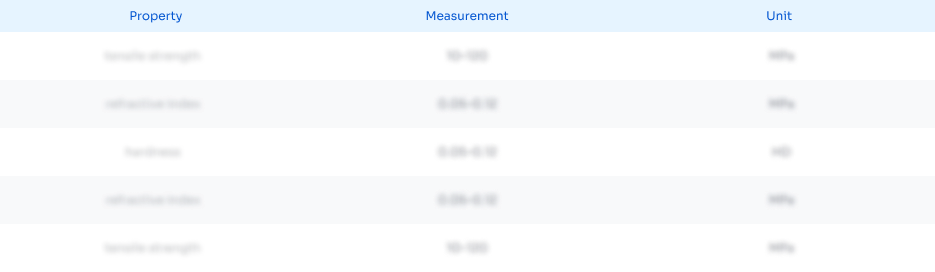
Abstract
Description
Claims
Application Information

- R&D
- Intellectual Property
- Life Sciences
- Materials
- Tech Scout
- Unparalleled Data Quality
- Higher Quality Content
- 60% Fewer Hallucinations
Browse by: Latest US Patents, China's latest patents, Technical Efficacy Thesaurus, Application Domain, Technology Topic, Popular Technical Reports.
© 2025 PatSnap. All rights reserved.Legal|Privacy policy|Modern Slavery Act Transparency Statement|Sitemap|About US| Contact US: help@patsnap.com