Hydraulic system having an adjustable hydrostatic machine
a hydrostatic machine and hydrostatic system technology, which is applied in the direction of machines/engines, positive displacement liquid engines, pump parameters, etc., can solve the problem of inability to centralize the adjusting piston, and achieve the effect of reducing the adjusting pressure, preventing the intake problem, and simplifying the mechanical coupling
- Summary
- Abstract
- Description
- Claims
- Application Information
AI Technical Summary
Benefits of technology
Problems solved by technology
Method used
Image
Examples
Embodiment Construction
[0030]In accordance with a first exemplified embodiment, the hydrostatic system 1 in accordance with the invention comprises a hydrostatic machine 2. The hydrostatic machine 2 is designed as a pump / motor machine. The hydrostatic machine 2 is designed to be adjustable in terms of its displaced volume and is preferably a hydrostatic axial piston machine in a swash-plate construction which can be pivoted out of a neutral position in two directions. The displaced volume is adjusted by an adjustment of the swash-plate. In the illustrated example, the hydrostatic machine 2 is connected to a first working line 3 and a second working line 4. The first working line 3 connects the hydrostatic machine 2 to a hydraulic accumulator 6. In contrast, the second working line 4 is connected to a tank volume 7. Alternatively, a high pressure accumulator can also be provided as a hydraulic accumulator 6 and a low pressure accumulator can be provided instead of the tank volume 7.
[0031]The hydrostatic ma...
PUM
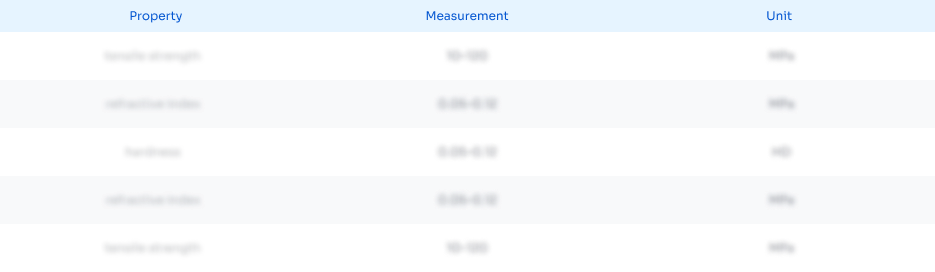
Abstract
Description
Claims
Application Information

- R&D
- Intellectual Property
- Life Sciences
- Materials
- Tech Scout
- Unparalleled Data Quality
- Higher Quality Content
- 60% Fewer Hallucinations
Browse by: Latest US Patents, China's latest patents, Technical Efficacy Thesaurus, Application Domain, Technology Topic, Popular Technical Reports.
© 2025 PatSnap. All rights reserved.Legal|Privacy policy|Modern Slavery Act Transparency Statement|Sitemap|About US| Contact US: help@patsnap.com