Methods for creating multi-walled containers and articles produced there from
a multi-walled container and container technology, applied in the field of methods for creating multi-walled containers and articles produced there, can solve the problem of formidable challenge of handling such large-format blanks
- Summary
- Abstract
- Description
- Claims
- Application Information
AI Technical Summary
Benefits of technology
Problems solved by technology
Method used
Image
Examples
Embodiment Construction
[0029]The following discussion is presented to enable a person skilled in the art to make and use the invention. Various modifications to the embodiments shown herein will be readily apparent to those skilled in the art, and the generic principles herein may be applied to other embodiments and applications without departing from the spirit and scope of the present invention, as defined by the appended claims. Thus, the present invention is not intended to be limited to the embodiments shown, but is to be accorded the widest scope consistent with the principles and features disclosed herein.
[0030]Turning then to the several Figures, where like numerals indicate like parts, and more particularly to FIGS. 1-4, an embodiment of the invention employing many of the features and elements of the invention will now be described. Container 20 comprises “blank”22, which is preferably constructed from a double lined, single wall corrugated material such as 5 / 16″ L flute corrugated board shown i...
PUM
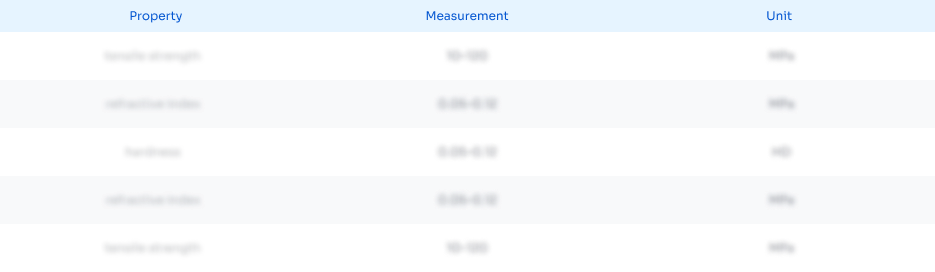
Abstract
Description
Claims
Application Information

- R&D
- Intellectual Property
- Life Sciences
- Materials
- Tech Scout
- Unparalleled Data Quality
- Higher Quality Content
- 60% Fewer Hallucinations
Browse by: Latest US Patents, China's latest patents, Technical Efficacy Thesaurus, Application Domain, Technology Topic, Popular Technical Reports.
© 2025 PatSnap. All rights reserved.Legal|Privacy policy|Modern Slavery Act Transparency Statement|Sitemap|About US| Contact US: help@patsnap.com