Dual thermodynamic cycle cryogenically fueled systems
a technology of thermodynamic cycle and cryogenic fluid, which is applied in the direction of mechanical equipment, machines/engines, lighting and heating apparatus, etc., can solve the problems of increasing the expansion process, the inefficient production of mechanical power from the phase change of the cryogenic fluid to the expanding gas, and the inability to use the phase change in the cryogenic fluid to achieve the expansion process. , to achieve the effect of reducing the expansion process, and increasing the energy of the second gas
- Summary
- Abstract
- Description
- Claims
- Application Information
AI Technical Summary
Problems solved by technology
Method used
Image
Examples
Embodiment Construction
[0028] Embodiments of the invention can be constructed from commercially available components. In all of the embodiments disclosed below, different materials could be used for the chambers and reservoirs, including but not exclusively including: various plastics, rubbers, resins, ceramics, and metals. In all of the embodiments disclosed below, different materials could be used for the piping, including but not exclusively including: various plastics, rubbers, resins, ceramics, metals, or other equivalent manmade materials. The heat exchanger could be a low-temperature heat exchanger, a mid-temperature heat exchanger, a high-temperature heat exchanger, or a combination of different types of heat exchangers.
[0029]FIG. 1 illustrates a block diagram of a conventional open Rankine cycle liquid nitrogen engine that has been extensively studied at the University of Washington. As shown, the engine has a heat source supplying heat 103 to a heat exchanger 102 that is connected with a pipe 1...
PUM
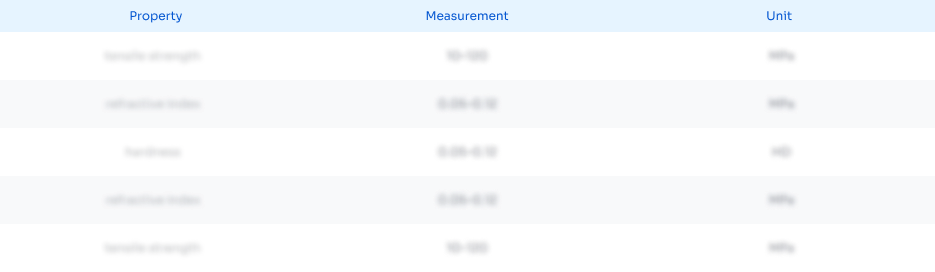
Abstract
Description
Claims
Application Information

- R&D
- Intellectual Property
- Life Sciences
- Materials
- Tech Scout
- Unparalleled Data Quality
- Higher Quality Content
- 60% Fewer Hallucinations
Browse by: Latest US Patents, China's latest patents, Technical Efficacy Thesaurus, Application Domain, Technology Topic, Popular Technical Reports.
© 2025 PatSnap. All rights reserved.Legal|Privacy policy|Modern Slavery Act Transparency Statement|Sitemap|About US| Contact US: help@patsnap.com