Heat exchangers with corrugated heat exchange elements of improved strength
a technology of heat exchange elements and corrugated sheets, which is applied in the direction of tubular elements, lighting and heating apparatuses, laminated elements, etc., can solve the problems of poor heat transfer, limited heat transfer, and relatively large space between adjacent side walls
- Summary
- Abstract
- Description
- Claims
- Application Information
AI Technical Summary
Benefits of technology
Problems solved by technology
Method used
Image
Examples
Embodiment Construction
[0032] The following is a detailed description of preferred corrugated heat exchange elements according to the invention, as well as preferred heat exchangers in which they are used. As used herein, the term “corrugated heat exchange element” is intended to include both corrugated fins and turbulizers which, as mentioned above, are structurally similar and differ primarily in the way they are incorporated into heat exchangers.
[0033] A first preferred corrugated heat exchange element 10 according to the invention is now described with reference to FIGS. 1 to 4. Heat exchange element 10 comprises a plurality of corrugations 11 extending along a longitudinal axis A, the corrugations 11 being defined by a plurality of spaced-apart side walls 12 interconnected by a plurality of top and bottom walls 14, 16. Each side wall 12 defines a plane S (FIG. 2) and extends parallel to axis A. Each of the side walls 12 has a height H and extends between an adjacent top wall 14 and an adjacent botto...
PUM
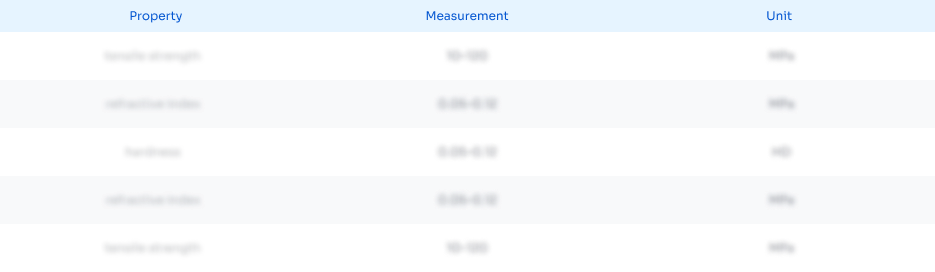
Abstract
Description
Claims
Application Information

- R&D
- Intellectual Property
- Life Sciences
- Materials
- Tech Scout
- Unparalleled Data Quality
- Higher Quality Content
- 60% Fewer Hallucinations
Browse by: Latest US Patents, China's latest patents, Technical Efficacy Thesaurus, Application Domain, Technology Topic, Popular Technical Reports.
© 2025 PatSnap. All rights reserved.Legal|Privacy policy|Modern Slavery Act Transparency Statement|Sitemap|About US| Contact US: help@patsnap.com