Heat exchanger support system and associated heat exchanger module
a technology of heat exchanger and support system, which is applied in the direction of stationary conduit assembly, stationary tubular conduit assembly, engine cooling apparatus, etc., can solve the problems of high cost increase fabrication cost, and introduce the risk of breakage of fixing or attachment elements, so as to achieve easy disassembly
- Summary
- Abstract
- Description
- Claims
- Application Information
AI Technical Summary
Benefits of technology
Problems solved by technology
Method used
Image
Examples
Embodiment Construction
[0041]FIG. 1 shows an exploded view in perspective of a heat exchange module comprising a support frame 2 according to the present invention, and FIG. 2 shows a front view in perspective of this frame. The frame 2, rectangular in shape, comprises two long sides and two short sides. The top long side comprises a lateral horizontal face 4 and the bottom long side comprises a lateral horizontal face 6. The short sides comprise lateral vertical faces, 8 and 10 respectively. The long sides also comprise front faces, 12 and 14 respectively, while the short sides comprise front faces 16 and 18 respectively. Finally, the top long side of the frame comprises an inclined face 19 placed between the lateral horizontal face 4 and the front face 12. As can be seen more particularly in FIG. 3, which shows the frame in section, the horizontal face 10 comprises stiffening ribs 20.
[0042] The frame is divided into two portions by a vertical upright 22 which delimits a large opening 24 and a small ope...
PUM
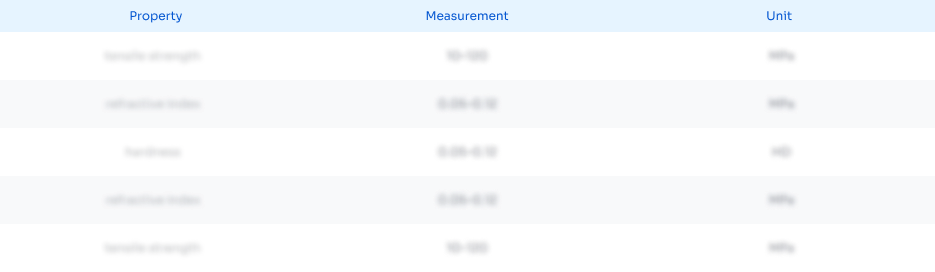
Abstract
Description
Claims
Application Information

- R&D
- Intellectual Property
- Life Sciences
- Materials
- Tech Scout
- Unparalleled Data Quality
- Higher Quality Content
- 60% Fewer Hallucinations
Browse by: Latest US Patents, China's latest patents, Technical Efficacy Thesaurus, Application Domain, Technology Topic, Popular Technical Reports.
© 2025 PatSnap. All rights reserved.Legal|Privacy policy|Modern Slavery Act Transparency Statement|Sitemap|About US| Contact US: help@patsnap.com