Working machine driving unit
a driving unit and working machine technology, applied in the direction of servomotors, instruments, analogue processes for specific applications, etc., can solve the problems of large-scale production costs, small and more unstable torques, and disadvantages of conventional systems, so as to reduce production costs, effectively share excess energy generated, and make up shortfalls in hydraulic fluid
- Summary
- Abstract
- Description
- Claims
- Application Information
AI Technical Summary
Benefits of technology
Problems solved by technology
Method used
Image
Examples
Embodiment Construction
[0031] The present invention is explained in detail, referring to an embodiment shown in FIGS. 1 through 3, another embodiment shown in FIG. 4, and a further embodiment shown in FIG. 5, other embodiments are shown in FIGS. 6 and 7, and another embodiment is shown in FIG. 8. The explanation of the hydraulic excavator shown in FIG. 9 is also used in the explanation of the present embodiments.
[0032]FIG. 1 shows an embodiment of a driving device of a work machine, which is a construction machine, or more precisely, a hydraulic excavator. As shown in FIG. 9, the hydraulic excavator has a working unit 6 comprising a boom 3, a stick 4, and a bucket 5 that are connected sequentially. Shown in FIG. 1 is a circuit diagram of a composite hybrid driving device of the hydraulic excavator. The driving device includes a boom-stick-bucket composite circuit. FIG. 2 shows a circuit diagram that illustrates the circuit diagram of FIG. 1 in more concrete terms.
[0033] As shown in FIG. 1, the working u...
PUM
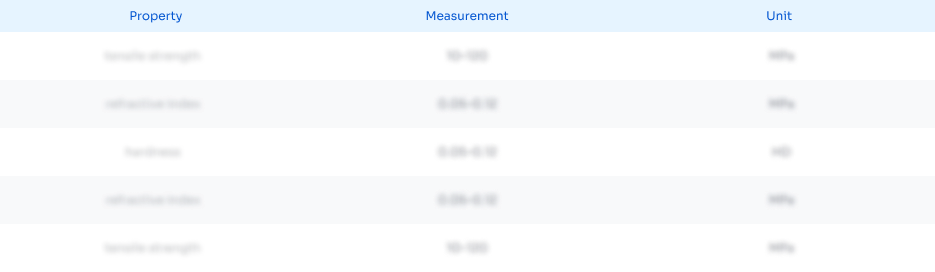
Abstract
Description
Claims
Application Information

- R&D
- Intellectual Property
- Life Sciences
- Materials
- Tech Scout
- Unparalleled Data Quality
- Higher Quality Content
- 60% Fewer Hallucinations
Browse by: Latest US Patents, China's latest patents, Technical Efficacy Thesaurus, Application Domain, Technology Topic, Popular Technical Reports.
© 2025 PatSnap. All rights reserved.Legal|Privacy policy|Modern Slavery Act Transparency Statement|Sitemap|About US| Contact US: help@patsnap.com