Golf club shaft having multiple metal fiber layers
a golf club shaft and metal fiber technology, applied in the field of composite resin/fiber golf club shafts, can solve the problems of difficult to overcome the design problems of conventional fiber reinforced resin technology, difficult to achieve conventional technology, and high cost of methods, so as to achieve high modulus of elasticity, increase kick, and increase mass
- Summary
- Abstract
- Description
- Claims
- Application Information
AI Technical Summary
Benefits of technology
Problems solved by technology
Method used
Image
Examples
Embodiment Construction
[0021] The following is a detailed description of the best presently known modes of carrying out the invention. This description is not to be taken in a limiting sense, but is made merely for the purpose of illustrating the general principles of the invention. The scope of the invention is defined by the appended claims.
[0022] As illustrated for example in FIG. 1, a golf club shaft 10 in accordance with a preferred embodiment of the present invention includes a hollow shaft 12, a grip 14, and a club head 16. The exemplary shaft 12 is divided into three sections—the grip section 18 which is covered by the grip 14, the tip section 20 which supports the club head 16, and the main body section 22 which extends from the distal end of the grip section to the proximal end of the tip section. In the illustrated embodiment, the grip section 18 is substantially cylindrical, the tip section 20 is substantially cylindrical, and the main body section 22 has a substantially constant taper. The p...
PUM
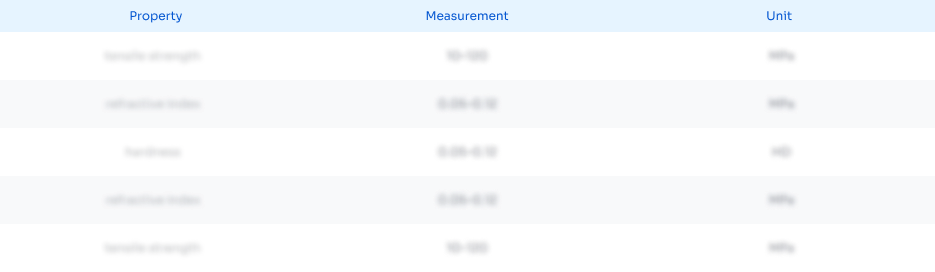
Abstract
Description
Claims
Application Information

- R&D
- Intellectual Property
- Life Sciences
- Materials
- Tech Scout
- Unparalleled Data Quality
- Higher Quality Content
- 60% Fewer Hallucinations
Browse by: Latest US Patents, China's latest patents, Technical Efficacy Thesaurus, Application Domain, Technology Topic, Popular Technical Reports.
© 2025 PatSnap. All rights reserved.Legal|Privacy policy|Modern Slavery Act Transparency Statement|Sitemap|About US| Contact US: help@patsnap.com