Heating oven for dynamo-electric machine component manufacture
a technology of dynamo-electric machines and components, which is applied in the direction of heat generation devices, dynamo-electric machines, heating fuel, etc., can solve the problems of mechanical wound wires, generating electromechanical forces that tend to loosen or deform the shape of wire coils, and generating vibration and heat. , to achieve the effect of streamlining air flow and minimizing or reducing air flow dead spaces
- Summary
- Abstract
- Description
- Claims
- Application Information
AI Technical Summary
Benefits of technology
Problems solved by technology
Method used
Image
Examples
Embodiment Construction
[0024] The present disclosure provides solutions for uniform and reproducible manufacturing of dynamo-electric machine components. A disclosed solution concerns heating furnaces or ovens, which may be used for heating batches of dynamo-electric machine component subassemblies, which have wire coil portions, to elevated processing temperatures.
[0025] The disclosed solution may find application in dynamo-electric machine component manufacturing processes where inter- or intra-component processing temperature uniformity is an important process parameter. The disclosed heating furnaces or ovens may be used, for example, as ovens to preheat dynamo-electric machine component subassemblies in preparation for resin application, or as resin-curing ovens. The furnaces or ovens may be integrated into a manufacturing assembly line by the use of suitable conveyor apparatus and component transfer devices. The conveyor apparatus may, for example, carry the component subassemblies in pallets place...
PUM
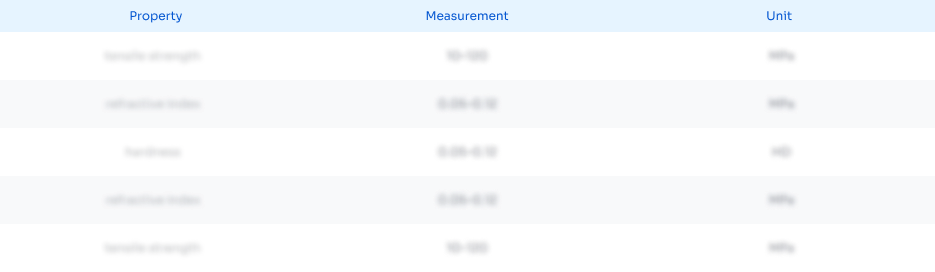
Abstract
Description
Claims
Application Information

- R&D
- Intellectual Property
- Life Sciences
- Materials
- Tech Scout
- Unparalleled Data Quality
- Higher Quality Content
- 60% Fewer Hallucinations
Browse by: Latest US Patents, China's latest patents, Technical Efficacy Thesaurus, Application Domain, Technology Topic, Popular Technical Reports.
© 2025 PatSnap. All rights reserved.Legal|Privacy policy|Modern Slavery Act Transparency Statement|Sitemap|About US| Contact US: help@patsnap.com