Industrial robot with controlled flexibility and simulated force for automated assembly
a robot and automation technology, applied in the direction of electric programme control, program control, instruments, etc., can solve the problems of repetitive motion stress injuries and injuries, problems with maintaining quality, efficiency, job satisfaction and health, and the robot positioning accuracy is not that relevant by itsel
- Summary
- Abstract
- Description
- Claims
- Application Information
AI Technical Summary
Benefits of technology
Problems solved by technology
Method used
Image
Examples
Embodiment Construction
)
[0016]FIG. 1 illustrates a preferred embodiment of the robotic system that can be easily programmed for assembly tasks.
[0017] Shown in FIG. 1 is an articulated industrial robot 10 interfaced with a computer controller 12 where the method of the present invention is implemented. Computer controller 12 comprises joint velocity controller 12a, admittance control 12b and for each articulated joint 10a of robot 10 a mechanical actuation device or drive 12c and a motion measurement 12d. Not shown in FIG. 1 is the processor which is part of controller 12.
[0018] In a typical industrial robot, there are four to seven articulated joints and when controlled synchronously, the end-effector 15 of the robot 10 can move in a three dimensional task space and follow a pre-designed trajectory. As described above, each joint would have its own mechanical actuation device or drive 12c, typically a servomotor, and measurement device 12d, typically a resolver or encoder to measure the joint angle. The...
PUM
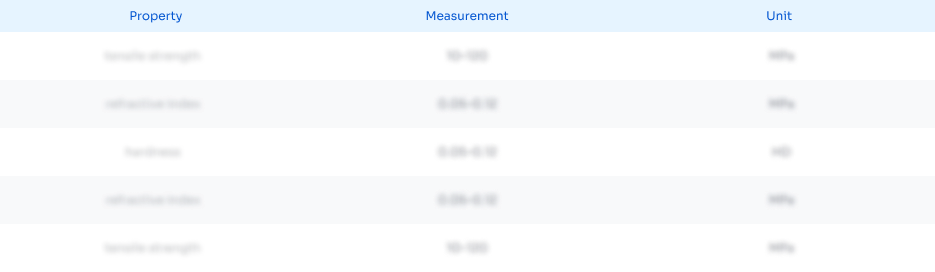
Abstract
Description
Claims
Application Information

- R&D
- Intellectual Property
- Life Sciences
- Materials
- Tech Scout
- Unparalleled Data Quality
- Higher Quality Content
- 60% Fewer Hallucinations
Browse by: Latest US Patents, China's latest patents, Technical Efficacy Thesaurus, Application Domain, Technology Topic, Popular Technical Reports.
© 2025 PatSnap. All rights reserved.Legal|Privacy policy|Modern Slavery Act Transparency Statement|Sitemap|About US| Contact US: help@patsnap.com