Ceramic end effector for micro circuit manufacturing
a technology of end effector and micro-circuit, which is applied in the direction of program-controlled manipulators, thin material processing, article separation, etc., can solve the problems of metal contamination within the processing chamber, high temperature of the thermal process, so as to achieve low cost
- Summary
- Abstract
- Description
- Claims
- Application Information
AI Technical Summary
Benefits of technology
Problems solved by technology
Method used
Image
Examples
Embodiment Construction
[0021]FIG. 1 shows an overview of an end effector 20 installed on a typical wafer handling robot 15 that is loading an RTP machine 30. The end effector 20 grips a wafer 17 and installs it through a slot 36 into the RTP processing chamber. Upon completion of the thermal process, the end effector is inserted into the processing chamber and retrieves the wafer 17 for transport to the next step in fabrication.
[0022]FIGS. 2-6 show the end effector 20 according to the present invention in more detail. The end effector 20 includes a body portion 25 that is made of a ceramic material such as, alumina, or silicon carbide, but preferably alumina. The body portion 25 is generally planar in shape and features a robot arm mounting end 19, and two outer wafer engaging fingers 27 and a center wafer support finger 29 at an axial end. The outer wafer engaging fingers 27 and support 29 each have a wafer support pad cavity which houses a wafer support pad that support the wafer during handling withou...
PUM
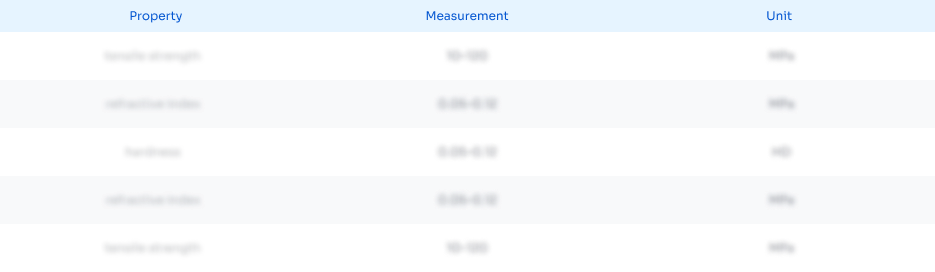
Abstract
Description
Claims
Application Information

- R&D
- Intellectual Property
- Life Sciences
- Materials
- Tech Scout
- Unparalleled Data Quality
- Higher Quality Content
- 60% Fewer Hallucinations
Browse by: Latest US Patents, China's latest patents, Technical Efficacy Thesaurus, Application Domain, Technology Topic, Popular Technical Reports.
© 2025 PatSnap. All rights reserved.Legal|Privacy policy|Modern Slavery Act Transparency Statement|Sitemap|About US| Contact US: help@patsnap.com