Anchorless electrostatically activated micro electromechanical system switch
an electrostatic activation and micro-electromechanical technology, applied in the field of switches, can solve the problems of slow switching speed, relatively high actuation voltage, and none of the above features of conventional switches
- Summary
- Abstract
- Description
- Claims
- Application Information
AI Technical Summary
Benefits of technology
Problems solved by technology
Method used
Image
Examples
Embodiment Construction
[0024] Referring now to the drawings in which like numerals reference like parts, FIGS. 1-2A show an exemplary MEMS switch 10 according to a first preferred embodiment. Referring to FIG. 1, the MEMS switch 10 includes a substrate 12 such as, for example, GaAs, quartz, or lithium niobate. However, the substrate 12 may also be transparent depending on the particular application intended for the MEMS switch 10. A beam 14 (stress free beam) is disposed above the substrate 12 and is provided within a first platform 16 and a second platform 18. The first and second platforms 16, 18 are also disposed on the substrate 12. The stress free beam 14 is not anchored to the first platform 16 or the second platform 18. Hence, the beam 14 is stress free and is therefore referred to as a “stress free beam.”
[0025] The stress free beam 14 is manufactured from a highly conductive material such as, for example, gold or tungsten and is displaceable in directions substantially parallel to the substrate 12...
PUM
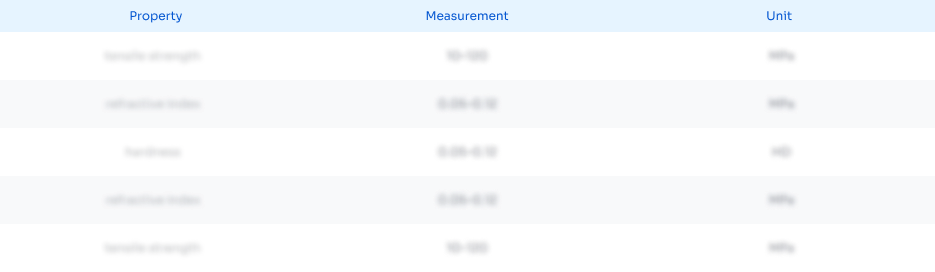
Abstract
Description
Claims
Application Information

- R&D
- Intellectual Property
- Life Sciences
- Materials
- Tech Scout
- Unparalleled Data Quality
- Higher Quality Content
- 60% Fewer Hallucinations
Browse by: Latest US Patents, China's latest patents, Technical Efficacy Thesaurus, Application Domain, Technology Topic, Popular Technical Reports.
© 2025 PatSnap. All rights reserved.Legal|Privacy policy|Modern Slavery Act Transparency Statement|Sitemap|About US| Contact US: help@patsnap.com