Monolithic pour joint
a monolithic, pour joint technology, applied in the direction of roads, constructions, paving details, etc., can solve the problems of small decrease in the overall volume of concrete, cracks may occur, large cracks may develop in concrete, etc., to prevent buckling or relative angular or vertical displacement of slabs, prevent unevenness or steps
- Summary
- Abstract
- Description
- Claims
- Application Information
AI Technical Summary
Benefits of technology
Problems solved by technology
Method used
Image
Examples
Embodiment Construction
[0028] Referring now to the drawings wherein the showings are for purposes of illustrating preferred embodiments of the present invention and not for purposes of limiting the same, FIG. 1 illustrates a monolithic pour joint 10 of the present invention wherein the pour joint 10 may be interposed between concrete slabs 12 that are disposed above a subgrade or a substrate 14. The substrate 14 may be soil underlying the slab. Alternatively, the substrate 14 may be a metal decking or other underlying surface adapted to support concrete slabs 12. The pour joint 10 is comprised of at least one elongate form 16 or a plurality of forms 16 arranged in end-to-end alignment with a splice 60 interconnecting the forms 16 and a plurality of elongate stakes 48 secured to a side of the forms 16 to fixedly maintain or support the forms 16 above the substrate 14.
[0029] Each of the forms 16 includes a substantially planar, vertical panel 18 having an upper edge 20 and a lower edge 22 to define a form ...
PUM
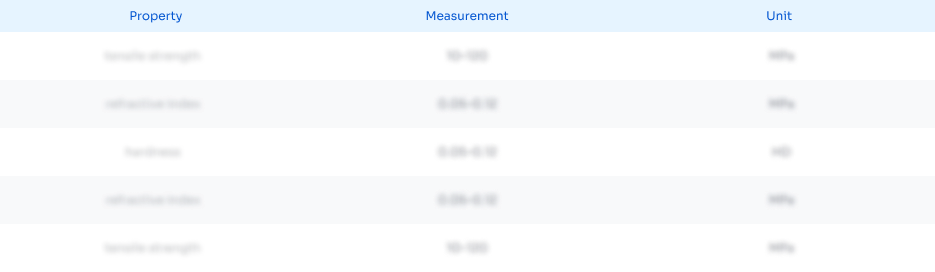
Abstract
Description
Claims
Application Information

- R&D
- Intellectual Property
- Life Sciences
- Materials
- Tech Scout
- Unparalleled Data Quality
- Higher Quality Content
- 60% Fewer Hallucinations
Browse by: Latest US Patents, China's latest patents, Technical Efficacy Thesaurus, Application Domain, Technology Topic, Popular Technical Reports.
© 2025 PatSnap. All rights reserved.Legal|Privacy policy|Modern Slavery Act Transparency Statement|Sitemap|About US| Contact US: help@patsnap.com