Measuring machine
a measuring machine and machine body technology, applied in the direction of electric/magnetic measuring arrangements, instruments, error compensation/elimination, etc., can solve the problems of uneven temperature distribution inside the machine, and deterioration of geometrical accuracy
- Summary
- Abstract
- Description
- Claims
- Application Information
AI Technical Summary
Benefits of technology
Problems solved by technology
Method used
Image
Examples
Embodiment Construction
)
[0045] An embodiment in which a measuring machine according to the present invention is applied to a three-dimensional measuring machine will be described below.
General Arrangement
[0046] As shown in FIG. 1, the three-dimensional measuring machine according to the present invention has a base 10, a touch signal probe P as a probe, a moving mechanism 20 for moving the touch signal probe P in three-dimensional directions (X, Y and Z-axis directions) relative to the base 10, and a controller 60 for controlling the movement of the moving mechanism 20 and for acquiring coordinates values of respective axes (X, Y and Z-axis) when the touch signal probe P contacts a workpiece to measure a dimension etc. of the workpiece based on the coordinates values.
[0047] The moving mechanism 20 has a column 21 and a supporter 22 disposed on both sides of the base 10 movably in back and forward direction (Y-axis direction), a X-beam 23 spanning over upper ends of the column 21 and the supporter 22, a sl...
PUM
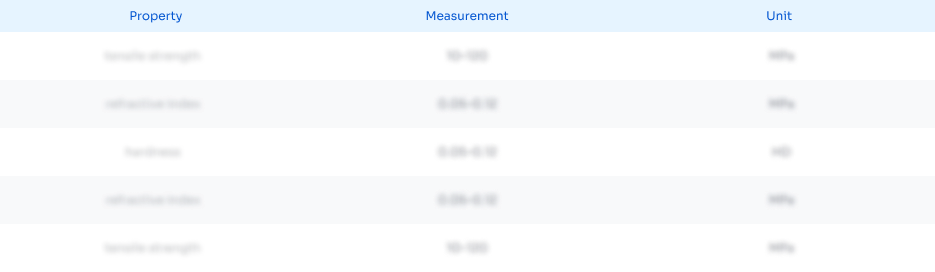
Abstract
Description
Claims
Application Information

- R&D
- Intellectual Property
- Life Sciences
- Materials
- Tech Scout
- Unparalleled Data Quality
- Higher Quality Content
- 60% Fewer Hallucinations
Browse by: Latest US Patents, China's latest patents, Technical Efficacy Thesaurus, Application Domain, Technology Topic, Popular Technical Reports.
© 2025 PatSnap. All rights reserved.Legal|Privacy policy|Modern Slavery Act Transparency Statement|Sitemap|About US| Contact US: help@patsnap.com