Waste heat boiler
A waste heat boiler and waste gas flow technology, which is applied to water heaters, fluid heaters, heat exchange equipment, etc., can solve the problems of hot spots on the exhaust chamber wall, shortened maintenance cycles, and shortened life of waste heat boilers, so as to avoid corrosion, Improve the service life, improve the function and the effect of life
- Summary
- Abstract
- Description
- Claims
- Application Information
AI Technical Summary
Problems solved by technology
Method used
Image
Examples
Embodiment Construction
[0024] FIG. 1 schematically shows a waste heat boiler 1 in longitudinal section. Such waste heat boilers are required for different chemical and petrochemical processes. The waste heat boiler 1 has a casing 2 which encloses a large number of heat transfer tubes 3 and a centrally arranged bypass tube 4, wherein the tubes 3, 4 are surrounded at their inlet and outlet ends 5, 6 by tube end plates 28 such that A cavity for conducting a cooling medium 31 for cooling the high-temperature exhaust gas flow 27 is formed in the housing 2 and the end plate 28 . The bypass pipe 4, which preferably has a larger diameter than the heat transfer pipe 3, can be partially or completely insulated over its length, so that the sometimes very high temperature exhaust gas 27 on the bypass pipe 4 cannot be conveyed too much to the cooling medium 31 The heat flows through the waste heat boiler 1. Viewed along the flow direction of the exhaust gas 27, that is, parallel to the longitudinal axis of the...
PUM
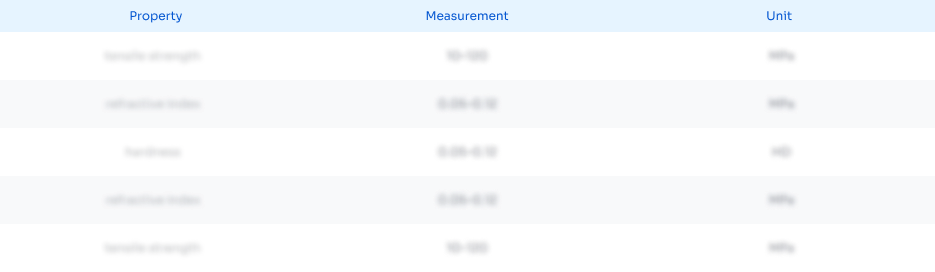
Abstract
Description
Claims
Application Information

- R&D
- Intellectual Property
- Life Sciences
- Materials
- Tech Scout
- Unparalleled Data Quality
- Higher Quality Content
- 60% Fewer Hallucinations
Browse by: Latest US Patents, China's latest patents, Technical Efficacy Thesaurus, Application Domain, Technology Topic, Popular Technical Reports.
© 2025 PatSnap. All rights reserved.Legal|Privacy policy|Modern Slavery Act Transparency Statement|Sitemap|About US| Contact US: help@patsnap.com