Formula for preparing dimension stone of magnesia alumina spinel by using sludge from factory of aluminum section, and preparation method
A magnesium aluminum spinel and aluminum profile factory technology, applied in the direction of alkaline earth aluminate/alumina/aluminum hydroxide preparation, etc., to achieve strong market competitiveness, improve product quality, and large surface area
- Summary
- Abstract
- Description
- Claims
- Application Information
AI Technical Summary
Problems solved by technology
Method used
Examples
preparation example Construction
[0012] The specific steps of the preparation method of the magnesium aluminum spinel material prepared from the sludge of an aluminum profile factory are as follows:
[0013] (A) According to the formula, put the aluminum profile factory sludge and basic magnesium carbonate in a ball mill and grind for 24 hours, raw materials: balls: water = 1: 1.5: 0.8, filter and dehydrate the ground slurry, and dry at 100 ° C for 24 hours and crushing to obtain less than 30 mesh aggregates.
[0014] (B) Adding (by weight) 6-8% water to the ground material for mixing, the mixing is uniform, and the mixing is subjected to semi-dry pressing.
[0015] (C) The preform is dried at 100°C for 24 hours.
[0016] (D) The dry blank is placed in a kiln for reaction sintering, the reaction sintering temperature is 1300-1650°C, the reaction sintering holding time is 1-8 hours, and naturally cooled to room temperature to obtain magnesia-aluminum spinel with a purity of 80-98%. Material.
Embodiment 1
[0018] The weight ratio of the raw material formula of this example: the aluminum profile factory sludge is 60%, basic magnesium carbonate is 40%. The two raw materials were weighed according to the formula, placed in a ball mill for wet grinding for 24 hours, raw materials: balls: water=1: 1.5: 0.8, the ground slurry was filtered and dehydrated, dried at 100°C for 24 hours, and crushed to obtain less than 30 purpose statistics. 6% water is added to the ground material for mixing, the mixing is uniform, and the mixture is semi-dry pressed. The molded billet was dried at 100°C for 24 hours, and the dry billet was placed in a kiln for reaction sintering at a reaction sintering temperature of 1400°C, a reaction sintering holding time of 4 hours, and naturally cooled to room temperature to obtain a synthetic magnesium aluminum spinel material.
Embodiment 2
[0020] The weight ratio of the raw material formula of this example: the aluminum profile factory sludge is 65%, basic magnesium carbonate is 35%. The two raw materials are weighed according to the formula, placed in a ball mill for wet grinding for 24 hours, raw materials: balls: water=1: 1.5: 0.8, the slurry to be ground is filtered and dehydrated, dried at 100°C for 24 hours and crushed to obtain less than 30 purpose statistics. 6% water is added to the ground material for mixing, the mixing is uniform, and the mixture is semi-dry pressed. The molded billet was dried at 100°C for 24 hours, and the dry billet was placed in a kiln for reaction sintering at a reaction sintering temperature of 1400°C and a reaction sintering holding time of 4 hours, then naturally cooled to room temperature to obtain a synthetic magnesium aluminum spinel material.
PUM
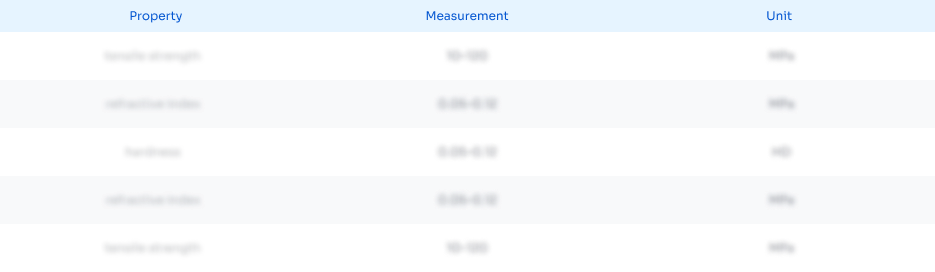
Abstract
Description
Claims
Application Information

- R&D
- Intellectual Property
- Life Sciences
- Materials
- Tech Scout
- Unparalleled Data Quality
- Higher Quality Content
- 60% Fewer Hallucinations
Browse by: Latest US Patents, China's latest patents, Technical Efficacy Thesaurus, Application Domain, Technology Topic, Popular Technical Reports.
© 2025 PatSnap. All rights reserved.Legal|Privacy policy|Modern Slavery Act Transparency Statement|Sitemap|About US| Contact US: help@patsnap.com