Method for raising fluidity of thermoplastic cross-linked rubber
A thermoplastic vulcanizate and fluidity technology, applied in the field of dynamic full vulcanization technology to prepare thermoplastic vulcanizate by melt blending, can solve the problems of increased hardness and compression deformation, decreased elasticity, etc., to improve fluidity and ensure dynamic vulcanization time Effect
- Summary
- Abstract
- Description
- Claims
- Application Information
AI Technical Summary
Benefits of technology
Problems solved by technology
Method used
Examples
Embodiment 1
[0022] An ethylene-propylene-diene monomer / polypropylene (EPDM / PP) blended thermoplastic vulcanizate with a rubber-to-plastic ratio of 60 / 40 was prepared (the plastics involved in premixing accounted for 30% of the total plastics).
[0023] The operation steps are as follows:
[0024] 1) Mix the plastics added for the first time: 20 grams of polypropylene, 0.67 grams of antioxidant (grade 1010) and rubber: 100 grams of EPDM rubber in a double-roller plastic mixer at 170 ° C (about 3 minutes ) to obtain the rubber-plastic premix, for subsequent use.
[0025] 2) Put the rubber-plastic premix prepared in the previous step into an internal mixer, add processing aids: 1.0 g of stearic acid, filler: 40 g of white carbon black, and knead for 1.5 minutes according to the rubber mixing method. Add softener: 100 grams of naphthenic oil, continue mixing for 2.5 minutes, finally add vulcanizing agent: 3 grams of dicumyl peroxide and accelerator: 1 gram of triallyl isocyanurate (TAIC) and...
Embodiment 2
[0029] Prepare a butyl rubber / polypropylene (IIR / PP) blended thermoplastic vulcanizate with a rubber-to-plastic ratio of 80 / 20 (the plastics involved in premixing account for 50% of the weight of the total plastics).
[0030] 1) Mix the plastics added for the first time: 12.5 grams of polypropylene, 0.25 grams of antioxidant (grade 1010) and rubber: 100 grams of butyl rubber at 170°C (about 3 minutes) to obtain a rubber and plastic premix, spare.
[0031] 2) Put the rubber-plastic premix prepared in the previous step into the internal mixer, add processing aids: 1.0 g of stearic acid, 40 g of filler: clay, knead for 1.5 minutes, and then add softening Agent: 100 grams of naphthenic oil, continue mixing for 2.5 minutes, finally add vulcanizing agent: 10.0 grams of tert-octyl phenolic resin and accelerator: 2.0 grams of stannous chloride and continue mixing for 1.5 minutes to make a vulcanization reaction material, which is set aside.
[0032] 3) Put the vulcanization reaction ...
Embodiment 3
[0035] Prepare a natural rubber / polyethylene (NR / PE) blended thermoplastic vulcanizate with a rubber-to-plastic ratio of 20 / 80 (the plastics involved in premixing account for 40% of the total plastic weight).
[0036] 1) Mix the plastics added for the first time: 160 grams of polyethylene, 4.0 grams of antioxidant (grade 1010) and rubber: 100 grams of natural rubber at 170°C (about 3 minutes) to obtain a rubber and plastic premix, which is set aside.
[0037] 2) Put the rubber-plastic premix prepared in the previous step into the internal mixer, add processing aids: 1.0 g of stearic acid, 40 g of filler: silica, mix for 1.5 minutes, and then add Softener: 100 grams of mixed oil of naphthenic oil and paraffin oil (mixing ratio is naphthenic oil: paraffin oil = 1: 1), continue mixing for 2.5 minutes, and finally add vulcanizing agent: 10.0 grams of tert-octyl phenolic resin and accelerator Agent: 2.0 grams of tin protochloride and continue mixing for 1.5 minutes to make a vulcan...
PUM
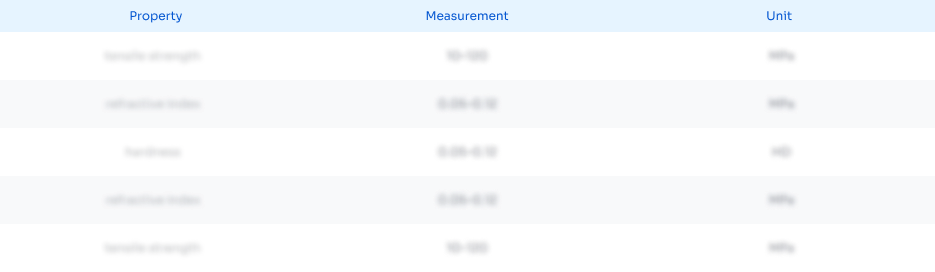
Abstract
Description
Claims
Application Information

- R&D
- Intellectual Property
- Life Sciences
- Materials
- Tech Scout
- Unparalleled Data Quality
- Higher Quality Content
- 60% Fewer Hallucinations
Browse by: Latest US Patents, China's latest patents, Technical Efficacy Thesaurus, Application Domain, Technology Topic, Popular Technical Reports.
© 2025 PatSnap. All rights reserved.Legal|Privacy policy|Modern Slavery Act Transparency Statement|Sitemap|About US| Contact US: help@patsnap.com