Anti-explosive container
A container and outer cylinder technology, applied in the field of anti-explosion containers, can solve the problems of small loading capacity, low impact resistance, short service life, etc., to reduce overpressure and noise, enhance impact resistance, and improve anti-explosion performance. Effect
- Summary
- Abstract
- Description
- Claims
- Application Information
AI Technical Summary
Problems solved by technology
Method used
Image
Examples
Embodiment Construction
[0013] The present invention will be further described below with reference to the accompanying drawings and examples.
[0014] Such as figure 1 As shown, the anti-explosion container has an outer cylinder 6, a fixed bottom plate 9, and a top cover 20. The inner side of the upper port of the outer cylinder 6 is provided with a spline collar 4, and the lower part of the outer cylinder 6 has a bottom head 7 welded therewith. The cover plate of the top cover 20 has an explosion vent hole 1 and is provided with a handle 2. The side wall of the top cover 20 and the inner side of the upper port of the outer cylinder 6 are matched by splines. The lower end of the top cover 20 is welded with a wave breaking plate 5 The lower part of the outer cylinder 6 is welded with a number of support vertical plates 8 welded and fixed with the fixed bottom plate 9. There is also an inner cylinder 10 in the outer cylinder 6. The inner cylinder 10 is composed of an inner top cover 13 and an inner cy...
PUM
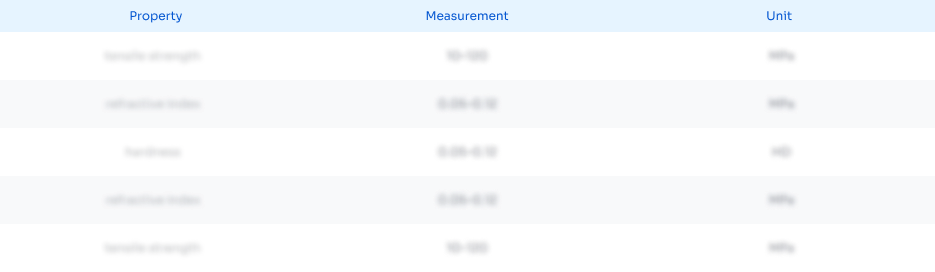
Abstract
Description
Claims
Application Information

- R&D Engineer
- R&D Manager
- IP Professional
- Industry Leading Data Capabilities
- Powerful AI technology
- Patent DNA Extraction
Browse by: Latest US Patents, China's latest patents, Technical Efficacy Thesaurus, Application Domain, Technology Topic, Popular Technical Reports.
© 2024 PatSnap. All rights reserved.Legal|Privacy policy|Modern Slavery Act Transparency Statement|Sitemap|About US| Contact US: help@patsnap.com