Variable printing machine
A printing press, variable technology, applied in printing presses, rotary printing presses, screen printing presses, etc., can solve the problems of inability to increase tension, easy to bump, unable to prevent snake spots, etc., to eliminate printing stains, eliminate bumps, etc. effect of injury
- Summary
- Abstract
- Description
- Claims
- Application Information
AI Technical Summary
Problems solved by technology
Method used
Image
Examples
Embodiment Construction
[0026] An example of the variable printing machine of the present invention consists of figure 2 with image 3 illustrate. In the figure with figure 1 The same components of the shown prior art are described with the same reference numerals.
[0027] Multiple sets (four sets) are arranged in the travel path between the feed rollers 1 and 2 on the upstream side and the downstream side of the continuous paper 10 in the traveling direction. The printing cylinder 4, the blanket cylinder 5, and the platen cylinder 6 constitute a variable printing machine. Printing units 3a, 3b, 3c, 3d. The printing cylinder 4 and the blanket cylinder 5 of each of the printing units 3a to 3d rotate at the same peripheral speed in the running direction of the continuous paper 10 . In addition, in figure 2 Not shown in the figure, a printing plate and a blanket are installed on the large-diameter outer peripheral surfaces of the printing cylinder 4 and the blanket cylinder 5, respectively. In ...
PUM
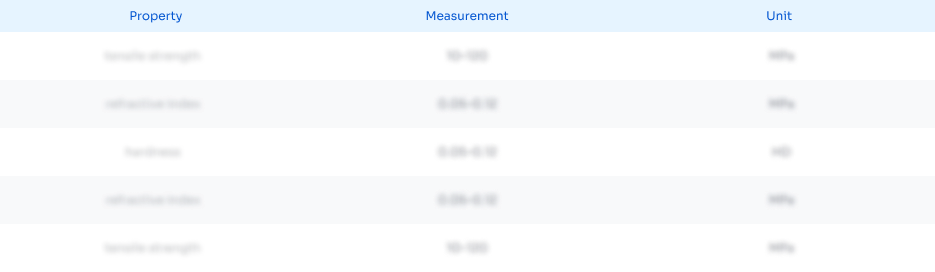
Abstract
Description
Claims
Application Information

- R&D Engineer
- R&D Manager
- IP Professional
- Industry Leading Data Capabilities
- Powerful AI technology
- Patent DNA Extraction
Browse by: Latest US Patents, China's latest patents, Technical Efficacy Thesaurus, Application Domain, Technology Topic, Popular Technical Reports.
© 2024 PatSnap. All rights reserved.Legal|Privacy policy|Modern Slavery Act Transparency Statement|Sitemap|About US| Contact US: help@patsnap.com