Flame retardant compositions for flammable plastics and flame retarded plastic compositions containing the same
A technology of flame retardant composition and flame retardant plastic, applied in the field of flame retardant composition, can solve problems such as not being universal, and achieve the effect of alleviating environmental concerns
- Summary
- Abstract
- Description
- Claims
- Application Information
AI Technical Summary
Problems solved by technology
Method used
Examples
Embodiment 1~20 and comparative example 1~19
[0093] 1. Preparation of test samples
[0094] According to the formulations shown in Tables 1-5, the various materials were blended and extruded with a twin-screw extruder to prepare pellets. The pellets were then injection molded into test specimens of predetermined size. The heating cylinder temperatures of the extruder and injection molding machine were set at the following temperatures.
[0095] plastic material
[0096] 2. Flame retardancy test
[0097] In Examples 1 to 16 and Comparative Examples 1 to 15, the vertical burning method according to the UL-94 standard was adopted. The size of the test sample is 125 mm in length, 12.5 mm in width and 3.2 mm in thickness. NR stands for Not Rated.
[0098] In Examples 17 to 20 and Comparative Examples 16 to 18, the oxygen index (LOI) was measured according to the JIS K 7201 standard test.
[0099] 3. Flexural strength
[0100] Flexural stress was determined according to ASTM-D 790.
[0101] 4. Evaluation aft...
Embodiment 21~26 and comparative example 20~23
[0114] 1. Preparation of foam samples
[0115] According to the formulation shown in Tables 7-8, each material except the blowing agent was loaded into a two-stage tandem extruder. The materials were heated and blended in a primary extruder with an inner diameter of 65 mm, and then extruded into a secondary extruder with an inner diameter of 90 mm. A predetermined amount of blowing agent is injected into the extrudate under pressure through a separate line located at the front end of the primary extruder. The extrudate from the primary extruder was cooled to 120° C. in the secondary extruder and extruded through a die into a ribbon having a width of 45 mm and a thickness of 2.5 mm.
[0116] 2. Visual evaluation of foam extrudates
[0117] The state of the obtained extrudate was visually evaluated according to the following criteria.
[0118] Good: A foam extrudate without cracks or voids was stably obtained.
[0119] Bad: The foam extrudate contains many cracks or voids, o...
Embodiment 27~30 and comparative example 24~26
[0131] 1. Preparation of test samples
[0132] According to the formulation shown in Table 9, all additives were mixed with the phenolic resin varnish. A sheet of kraft paper was impregnated with the resulting mixture and dried to prepare a prepreg. Then put 8 sheets of prepreg at 150kgf / cm in a hot press 2 Lamination was carried out under pressure at 150°C for 1 hour to prepare a paper-phenolic resin laminate having a thickness of 1.6 mm.
[0133] 2. Flame retardancy test
[0134] The vertical burning method according to the UL-95 standard was performed using a test sample 125 mm long, 12.5 mm wide and 3.2 mm thick. The results are shown in Table 9.
[0135] Recipe (number of servings) and test results
[0136] As shown in Table 9, the laminates of Examples 27-30 exhibited improved flame retardancy over the laminates of Comparative Examples 24-26.
PUM
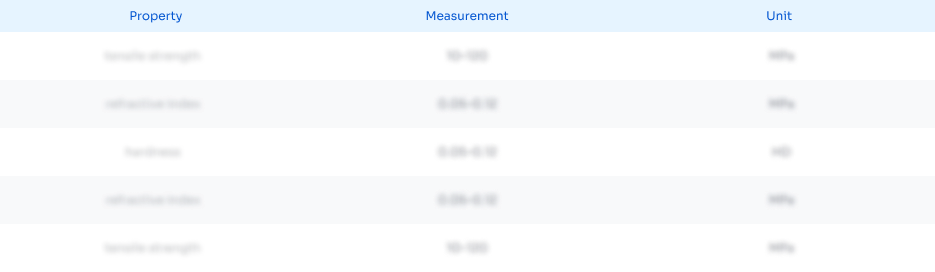
Abstract
Description
Claims
Application Information

- Generate Ideas
- Intellectual Property
- Life Sciences
- Materials
- Tech Scout
- Unparalleled Data Quality
- Higher Quality Content
- 60% Fewer Hallucinations
Browse by: Latest US Patents, China's latest patents, Technical Efficacy Thesaurus, Application Domain, Technology Topic, Popular Technical Reports.
© 2025 PatSnap. All rights reserved.Legal|Privacy policy|Modern Slavery Act Transparency Statement|Sitemap|About US| Contact US: help@patsnap.com