Microwave drying method of honeycomb formed bodies
A technology of microwave drying and sintering, which is applied in the directions of drying solid materials, heating to dry solid materials, and drying, etc., which can solve the problems of inability to obtain, difficult to fully reduce the drying speed difference, etc.
- Summary
- Abstract
- Description
- Claims
- Application Information
AI Technical Summary
Problems solved by technology
Method used
Image
Examples
Embodiment
[0066] The present invention will be described in more detail below based on examples, but the present invention is not limited to these examples.
reference example 1
[0068] After mixing talcum powder, pottery clay, bauxite, binder, water, etc., kneading (kneading) and soil refining (soil refining), use the obtained clay to make a diameter of 120mm and a length of 200mm by extrusion. , the wall thickness is about 100μm, and the number of compartments is about 300 / in 2 (about 46 / cm 2 ) honeycomb sintered body. The sintered body was arranged longitudinally (the axial direction of the compartment is the state of the up and down direction) in a batch type microwave drying oven (heating efficiency 0.5), and was irradiated with microwaves with a frequency of 2.45 GHz at an output density of 1 kW / kg for 300 seconds to dry . In addition, in this example, the ratio of the incident density of microwaves incident on the honeycomb sintered body from the vertical direction to the incident density from the horizontal direction is estimated to be about 1:1 (A / (A+B)0.5).
[0069] after drying, yes Figure 11 The outer peripheral portion 11 and the inn...
reference example 2
[0071] After mixing talcum powder, pottery clay, bauxite, binder, water, etc., kneading and smelting, use the obtained clay to make a diameter of 120mm, a length of 200mm, a wall thickness of about 100μm, and a The number of chambers is about 300 / in 2 (about 46 / cm 2 ) honeycomb sintered body. The sintered body was set longitudinally (the state where the axial direction of the compartment is the up-down direction) in a batch-type microwave drying oven (heating efficiency 0.5), and irradiated with microwaves with a frequency of 2.45 GHz at an output density of 0.5 kW / kg for 600 seconds to carry out dry. In addition, in this example, the ratio of the incident density of microwaves incident on the honeycomb sintered body from the vertical direction to the incident density from the horizontal direction is estimated to be about 1:1 (A / (A+B)0.5). after drying, yes Figure 11 The outer peripheral portion 11 and the inner portion 13 of the honeycomb sintered body 1 shown in , meas...
PUM
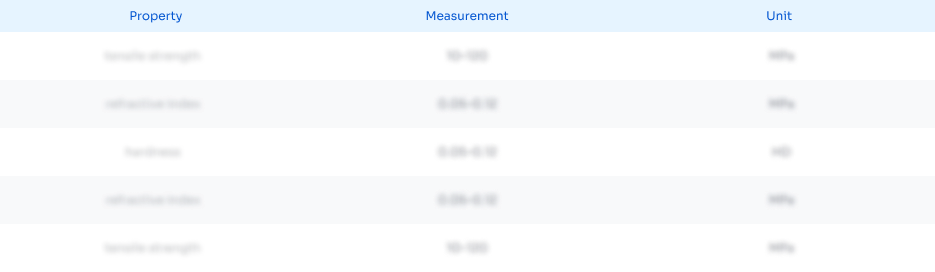
Abstract
Description
Claims
Application Information

- Generate Ideas
- Intellectual Property
- Life Sciences
- Materials
- Tech Scout
- Unparalleled Data Quality
- Higher Quality Content
- 60% Fewer Hallucinations
Browse by: Latest US Patents, China's latest patents, Technical Efficacy Thesaurus, Application Domain, Technology Topic, Popular Technical Reports.
© 2025 PatSnap. All rights reserved.Legal|Privacy policy|Modern Slavery Act Transparency Statement|Sitemap|About US| Contact US: help@patsnap.com