Ultrafine processing method of molybdenum disulfide powder
A technology of molybdenum disulfide and a processing method, applied in the direction of dyeing physical treatment, etc., can solve the problems such as the lack of purchasing ultra-fine molybdenum disulfide powder, and the preparation process of ultra-fine molybdenum disulfide powder that has not been reported, and achieves a solution to the problem of anti-coarse Effect
- Summary
- Abstract
- Description
- Claims
- Application Information
AI Technical Summary
Problems solved by technology
Method used
Image
Examples
Embodiment 1
[0022] Particle classification (micron)
Embodiment 2
[0024] Weigh 1000g of molybdenum disulfide coarse powder and put it into a stirring mill, then put in 5kgΦ5mm~10mm zirconia balls, then add 800ml of industrial ethanol, after ball milling for 40h, take out the slurry, dry and heat at 80°C. Put 1000g of dried molybdenum disulfide into a polyurethane ball mill tank, and then put it into a Φ30mm polyurethane core-spun ball, and continue ball milling for 2 hours to produce a finished product.
Embodiment 3
[0026] Weigh 1000g of molybdenum disulfide coarse powder and put it into the stirring mill, then put in 8kgΦ5mm~10mm zirconia balls, then add 900ml of industrial ethanol, after ball milling for 30h, take out the slurry, dry and heat at 80°C. Put 1000g of dried molybdenum disulfide into a polyurethane ball mill tank, and then put it into a Φ30mm polyurethane core-spun ball, and continue ball milling for 2 hours to produce a finished product.
PUM
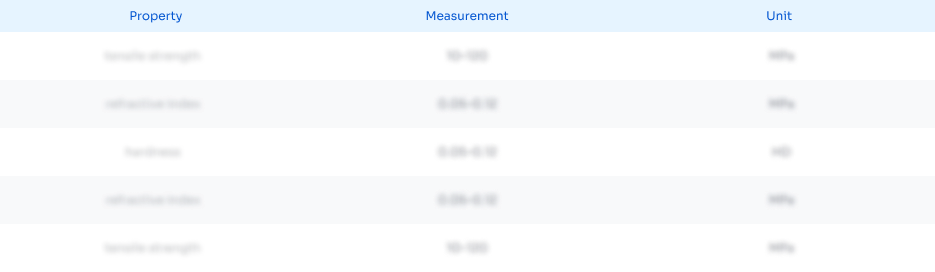
Abstract
Description
Claims
Application Information

- Generate Ideas
- Intellectual Property
- Life Sciences
- Materials
- Tech Scout
- Unparalleled Data Quality
- Higher Quality Content
- 60% Fewer Hallucinations
Browse by: Latest US Patents, China's latest patents, Technical Efficacy Thesaurus, Application Domain, Technology Topic, Popular Technical Reports.
© 2025 PatSnap. All rights reserved.Legal|Privacy policy|Modern Slavery Act Transparency Statement|Sitemap|About US| Contact US: help@patsnap.com