High-carbon high-alloy wearable steel ball
A manufacturing method and technology of wear-resistant steel, applied in the manufacture of the steel grinding ball, in the field of high-carbon and high-alloy steel grinding balls, can solve the problems of not meeting the requirements of large-scale grinding ball machines, shortening the life of the mill liner, wasting resources, etc. Problems, achieve good application effect and economic benefits, ideal combination of wear resistance and toughness, and improve economic benefits
- Summary
- Abstract
- Description
- Claims
- Application Information
AI Technical Summary
Problems solved by technology
Method used
Examples
Embodiment 1
[0008] Example 1: The chemical composition and weight ratio of the steel ball of the present invention are: 1.82 parts of C, 5.3 parts of Cr, 1.1 parts of Si, 0.59-1.0 parts of Mn, 0.058-0.15 parts of Mo, 0.038 parts of Cu, 0.59 parts of rare earth parts, S≤0.035 parts, P≤0.035 parts, and the rest is Fe.
[0009] The manufacturing method is as follows: mixing steel scrap with raw materials containing the chemical components described in claim 1, melting in an intermediate frequency electric furnace, and melting it when the temperature is raised to 1550°; then, taking a sample before the furnace for analysis, and adjusting the chemical components content to make it reach the proportioning relation of each composition described in claim 1, then carry out casting, and casting temperature is 1430 °; Then, carry out metal mold casting (circle); Then, cast the steel ball of molding at 300 ° Heat treatment at constant temperature for more than 20 hours between ~600°C to obtain Leysit...
Embodiment 2
[0010] Embodiment 2: The optimum ratio of the chemical composition of the steel ball of the present invention is: C 1.98 parts (by weight) Cr 6.8 parts (by weight) Si 1.5 parts (by weight) Mn 1.0 parts (by weight) ) Mo 0.15 parts (by weight) Cu 0.06 parts (by weight) Rare earth 0.72 parts (by weight) S 0.035 parts (by weight) P 0.035 parts (by weight).
[0011] Its manufacturing method is as follows: mix steel scrap with raw materials containing the above-mentioned chemical components, melt it in an intermediate frequency electric furnace, and heat it up to 1550° to melt it; then, take a sample before the furnace for analysis, and adjust the content of each chemical component to reach According to the proportioning relationship of each component described in claim 1, casting is then carried out at a casting temperature of 1430°; then, metal mold casting (circular shape) is carried out; then, the cast steel ball is placed between 300°~600° Heat treatment at constant temperature...
PUM
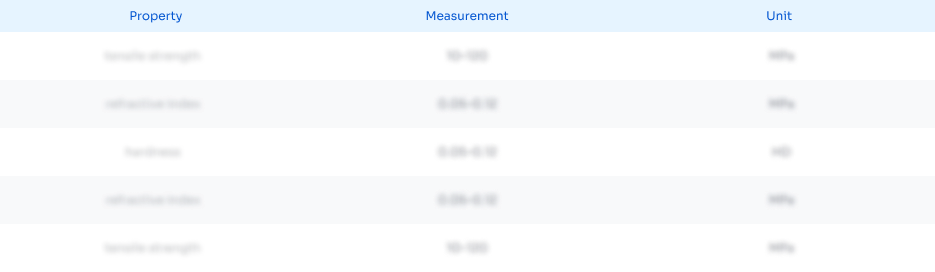
Abstract
Description
Claims
Application Information

- R&D Engineer
- R&D Manager
- IP Professional
- Industry Leading Data Capabilities
- Powerful AI technology
- Patent DNA Extraction
Browse by: Latest US Patents, China's latest patents, Technical Efficacy Thesaurus, Application Domain, Technology Topic, Popular Technical Reports.
© 2024 PatSnap. All rights reserved.Legal|Privacy policy|Modern Slavery Act Transparency Statement|Sitemap|About US| Contact US: help@patsnap.com