Polymeric creping adhesives and creping methods using same
A technology of adhesive and polymer, which is applied in the manufacture of crepe fiber paper web and crepe paper field, and can solve the problems of drying cylinder surface wear, uneven wrinkling, thickening, etc.
- Summary
- Abstract
- Description
- Claims
- Application Information
AI Technical Summary
Problems solved by technology
Method used
Image
Examples
Embodiment
[0075] in the following and image 3 and 4 The examples described and the results shown in the present invention demonstrate the superiority of the ionene adhesive formulations used in the present invention over conventional adhesive formulations. Table 1 below and image 3 and 4 The graph in the figure shows the results of comparative experiments. In an example, the formulation of Example 1 included a terpolymer ionene binder denoted "M", a water-based polyvinyl alcohol formulation denoted 2076 (which was obtained from Buckman Laboratories International, Inc.) and Busperse 2098 (an oil-based mold release agent, also available from Buckman Laboratories International, Inc.). The formulation of Comparative Example I contained polyvinyl alcohol (PVA), sorbitol and Triton X-100 (alkylphenol ethoxylate, 100% active). The machine used consisted of a ventilated dryer with felt on the cob side, debunizer on the table, 40-50% moisture in content, 10 % moisture out content, 16 foo...
PUM
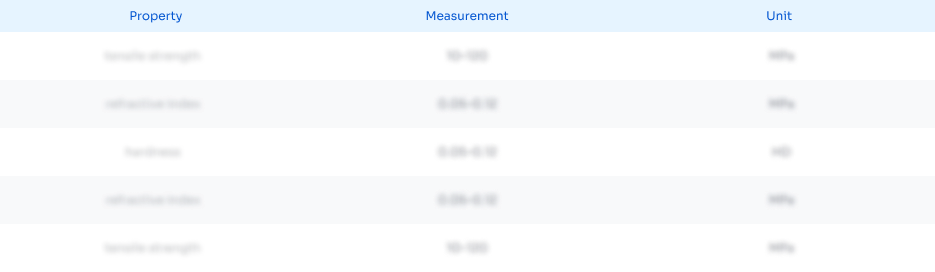
Abstract
Description
Claims
Application Information

- R&D
- Intellectual Property
- Life Sciences
- Materials
- Tech Scout
- Unparalleled Data Quality
- Higher Quality Content
- 60% Fewer Hallucinations
Browse by: Latest US Patents, China's latest patents, Technical Efficacy Thesaurus, Application Domain, Technology Topic, Popular Technical Reports.
© 2025 PatSnap. All rights reserved.Legal|Privacy policy|Modern Slavery Act Transparency Statement|Sitemap|About US| Contact US: help@patsnap.com