Torque beam suspension
A torque beam and suspension technology, which is applied in the direction of suspension, elastic suspension, transportation and packaging, etc., can solve the problems of difficult torsion deformation of torque beams, increased welding costs, and enlarged relative ends, etc., to increase toe-in rigidity , Improve the effect of welding accuracy
- Summary
- Abstract
- Description
- Claims
- Application Information
AI Technical Summary
Problems solved by technology
Method used
Image
Examples
Embodiment Construction
[0038] will now refer to Figure 1-10 The first embodiment of the present invention will be described.
[0039] as in figure 1 and 2 As shown in , the torque beam type suspension for the rear wheels of an automobile includes left and right trailing arms 10L and 10R extending in the longitudinal direction of the vehicle body, and torque beams extending in the transverse direction and interconnecting the left and right trailing arms 10L and 10R. Beam 11. Cylindrical trailing arm supports 12, 12 are welded to the front ends of the trailing arms 10L and 10R, and are hingedly supported by rubber sleeve joints (not shown) fitted in the trailing arm supports 12, 12 to carry on the vehicle body. Vertical swing motion. The left and right rear wheels W, W are rotatably supported on shafts 14, 14 fixed to shaft support plates 13, 13 welded to the rear outer ends of the trailing arms 10L and 10R. Spring seats 15, 15 for supporting the lower ends of the suspension springs are provided...
PUM
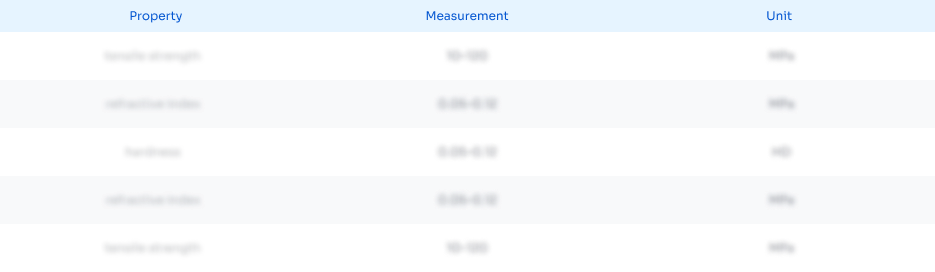
Abstract
Description
Claims
Application Information

- R&D
- Intellectual Property
- Life Sciences
- Materials
- Tech Scout
- Unparalleled Data Quality
- Higher Quality Content
- 60% Fewer Hallucinations
Browse by: Latest US Patents, China's latest patents, Technical Efficacy Thesaurus, Application Domain, Technology Topic, Popular Technical Reports.
© 2025 PatSnap. All rights reserved.Legal|Privacy policy|Modern Slavery Act Transparency Statement|Sitemap|About US| Contact US: help@patsnap.com