Process and device for continuous production of vanadium nitride alloy
A technology for vanadium nitride alloy and production device, applied in the field of iron and steel metallurgy, can solve the problems of no continuous production of vanadium nitride production process, non-continuous production method, large equipment investment, etc., and achieves easy control of production process and low cost. , The effect of less investment in equipment
- Summary
- Abstract
- Description
- Claims
- Application Information
AI Technical Summary
Problems solved by technology
Method used
Image
Examples
Embodiment
[0047] According to the production process of the present invention, 4 batches of vanadium nitride alloys were trial-produced on the device for continuous production of vanadium nitride alloys described in the present invention. The composition and ratio of the 4 batches of raw materials equipped are shown in Table 1. After the raw materials are prepared, the pellets enter the hopper through mixing, pressing, molding and drying. The size and drying parameters of the pellets are listed in Table 2. The pellets enter the reduction and nitriding vertical electric furnace from the hopper through the feed port, and then enter the reduction and nitriding section through the preheating section and the pre-reduction section. The temperature ranges of the pre-reduction section, the reduction nitriding section, and the nitrogen flow rate entering the reduction nitriding vertical electric furnace are listed in Table 3. Finally, vanadium nitride is produced through reduction nitriding in ...
PUM
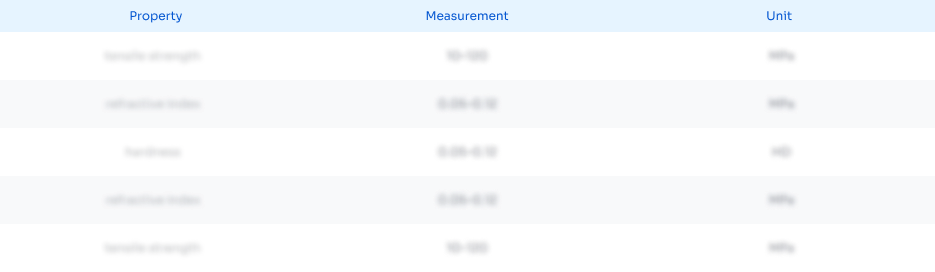
Abstract
Description
Claims
Application Information

- R&D
- Intellectual Property
- Life Sciences
- Materials
- Tech Scout
- Unparalleled Data Quality
- Higher Quality Content
- 60% Fewer Hallucinations
Browse by: Latest US Patents, China's latest patents, Technical Efficacy Thesaurus, Application Domain, Technology Topic, Popular Technical Reports.
© 2025 PatSnap. All rights reserved.Legal|Privacy policy|Modern Slavery Act Transparency Statement|Sitemap|About US| Contact US: help@patsnap.com