Felament machine sewing yarn
A technology of filament machine and filament yarn, which is applied in the direction of yarn, textiles, papermaking, and thin material processing, etc. It can solve the problems of uniformity deterioration, significant difference in dyeability, separation of two filament yarns, etc. The effect of sewing
- Summary
- Abstract
- Description
- Claims
- Application Information
AI Technical Summary
Problems solved by technology
Method used
Examples
Embodiment 1~4 and comparative example 1~3
[0041] Raw Yarn Preparation
[0042] PET containing 0.02% by weight of titanium dioxide was prepared as the polymer for polyester filament A; PET was prepared without a matting agent such as titanium dioxide as the polymer for polyester filament B. Both polymers were dried separately at 160°C for 4 hrs.
[0043] Then, both polymers were melted at 300°C. Then, by using a bisected spinneret, the polymer used for polyester filament A is discharged from 15 holes, and the polymer used for polyester filament B is discharged from 5 holes. Cool with air at room temperature and solidify in the side air quenching tunnel below. An oil agent was applied to the two kinds of yarns in a blended state, and then the resulting yarn was taken up at 1200 m / min, thereby providing a 180 dtex / 20 filament undrawn yarn. The undrawn yarn consisted of 144 decitex polyester filament A and 36 decitex polyester filament B.
[0044] The undrawn yarn was fed into a drawing machine and drawn under the fol...
Embodiment 5~7 and comparative example 4 and 5
[0057] Raw Yarn Preparation
[0058] PET was prepared as the polymer for polyester filament A without a matting agent such as titanium dioxide, and PET was prepared as a polymer for polyester filament B without a matting agent such as titanium dioxide. Both polymers were dried at 160° C. for 4 hrs, respectively.
[0059] Then, the polymer used for polyester filament B is mixed with polymethyl methacrylate (Delpet80N, manufactured by Asahi Kasei Industrial Co., Ltd.), and carried out in a sliced state. The amount of the latter is 0.5 to 8.0%. As an orientation inhibitor, use A screw melt extruder melts the two polymers at 300°C. The bisected spinneret is applied, and the polymer used for polyester filament A is extruded from 15 holes, and the polymer used for polyester filament B is discharged from 5 holes. Air cooling and solidification at room temperature in a side-blown quenching tunnel. The oil agent was applied to the two kinds of filaments in a blended state, and the...
PUM
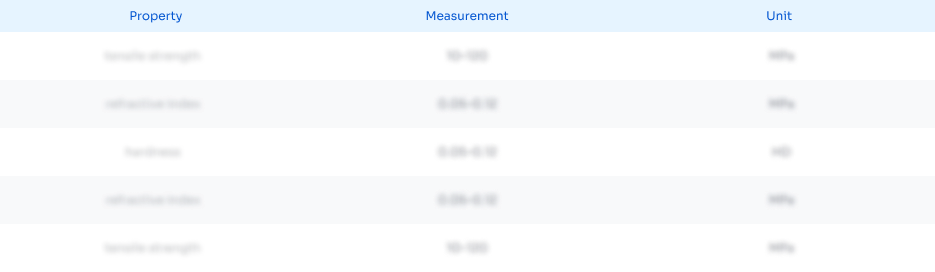
Abstract
Description
Claims
Application Information

- Generate Ideas
- Intellectual Property
- Life Sciences
- Materials
- Tech Scout
- Unparalleled Data Quality
- Higher Quality Content
- 60% Fewer Hallucinations
Browse by: Latest US Patents, China's latest patents, Technical Efficacy Thesaurus, Application Domain, Technology Topic, Popular Technical Reports.
© 2025 PatSnap. All rights reserved.Legal|Privacy policy|Modern Slavery Act Transparency Statement|Sitemap|About US| Contact US: help@patsnap.com