Linkage branch mechanism of parallel robot and six freedom parallel robot mechanism
A degree of freedom, robot technology, used in manipulators, program-controlled manipulators, manufacturing tools, etc., can solve the problems of low precision, large inertia, and low stiffness of end parts, and achieve the effect of increasing flexibility and improving stiffness.
- Summary
- Abstract
- Description
- Claims
- Application Information
AI Technical Summary
Problems solved by technology
Method used
Image
Examples
Embodiment Construction
[0020] figure 2 is a schematic diagram of the connection branch structure in the parallel robot mechanism of the embodiment of the present invention. As shown in the figure, the connection branch structure is composed of a ball hinge 32, a parallelogram mechanism 34 connected to the ball hinge 32 through an output rod 33, and a moving pair connected between the input rod 35 and the fixed platform 36 of the parallelogram mechanism. Between the parallel output and input rods are two connecting rods which are also parallel to each other. The "parallelogram mechanism" mentioned here refers to the mechanism formed by the input rod, the connecting rod, the output rod, and the connecting rod of the planar four-bar mechanism, which are connected by rotating pairs in sequence. The lengths of the two rods (that is, the input rod and the output rod, and the two connecting rods) are equal.
[0021] Motion platform 31 is connected on the output bar 33 of parallelogram mechanism 34 by ba...
PUM
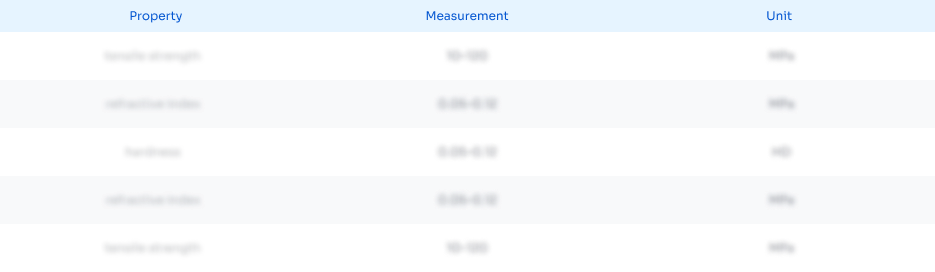
Abstract
Description
Claims
Application Information

- Generate Ideas
- Intellectual Property
- Life Sciences
- Materials
- Tech Scout
- Unparalleled Data Quality
- Higher Quality Content
- 60% Fewer Hallucinations
Browse by: Latest US Patents, China's latest patents, Technical Efficacy Thesaurus, Application Domain, Technology Topic, Popular Technical Reports.
© 2025 PatSnap. All rights reserved.Legal|Privacy policy|Modern Slavery Act Transparency Statement|Sitemap|About US| Contact US: help@patsnap.com