Low light loss matrix material for fibre-optical and its manufacturing method
A technology of base materials and manufacturing methods, applied in manufacturing tools, glass manufacturing equipment, optics, etc., can solve problems such as poor optical signal transmission quality
- Summary
- Abstract
- Description
- Claims
- Application Information
AI Technical Summary
Problems solved by technology
Method used
Image
Examples
experiment example 1
[0038] According to the vapor deposition (VAD) process, the porous matrix member can be formed by depositing glass particles. Then, the porous base member was hung vertically in the electric furnace. According to this configuration, in order to shape the optical fiber core member, the porous basic member is dehydrated at 1100°C in a chlorine and helium gas mixture atmosphere, purified at 1100°C in a 100% helium atmosphere, and then dehydrated in a 100% helium atmosphere Vitrification treatment at 1500°C.
[0039]The processing furnace used here includes a quartz tube. Porous or glass matrix material is placed in this quartz tube during operation, and the purpose is to ensure that the matrix material is sealed from the air when moving the matrix material up or down. A heater installed in the furnace heats a portion of the quartz tube. According to this configuration, the above-mentioned steps and processes are correspondingly completed when the base member passes through the...
PUM
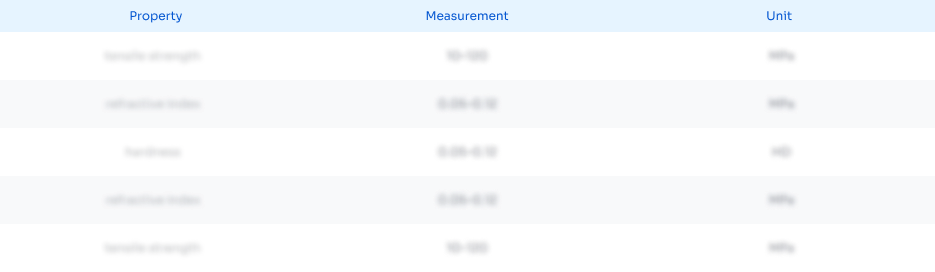
Abstract
Description
Claims
Application Information

- R&D
- Intellectual Property
- Life Sciences
- Materials
- Tech Scout
- Unparalleled Data Quality
- Higher Quality Content
- 60% Fewer Hallucinations
Browse by: Latest US Patents, China's latest patents, Technical Efficacy Thesaurus, Application Domain, Technology Topic, Popular Technical Reports.
© 2025 PatSnap. All rights reserved.Legal|Privacy policy|Modern Slavery Act Transparency Statement|Sitemap|About US| Contact US: help@patsnap.com